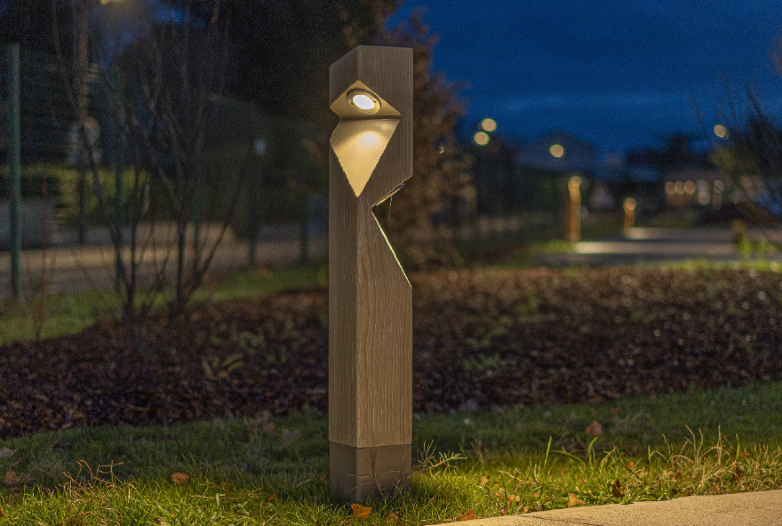
Dans ce deuxième volet consacré au « Fabriqué en France », nous avons interrogé six sociétés d’éclairage public : souvent entreprises familiales devenues de grands groupes, elles ont su garder ce savoir-faire patrimonial qui ont fait leur valeur.
Pour ce « Fabriqué en France » dédié à l’éclairage extérieur, nous avons donné la parole aux entreprises Lenzi, Groupe Ragni, Technilum, Aubrilam, Abel Eclairage et Selux, dont certaines sont labellisées « Entreprise du Patrimoine Vivant ». Depuis sa création en 2005, le label EPV met en lumière des entreprises uniques qui savent concilier l’innovation et la tradition, le savoir-faire et la création, le patrimoine et l’avenir, le local et l’international. Ce label d’État est rattaché au ministère de l’Économie, des Finances et de la Souveraineté industrielle et numérique, et il est décerné par les préfets de région. Attribué pour une période de cinq ans, le label EPV rassemble des fabricants partageant une certaine vision des activités qui doivent être celles de leur entreprise : une vision entrepreneuriale où le respect du caractère historique et patrimonial de l’entreprise et ses outils ne s’opposent en rien, mais viennent plutôt nourrir la qualité de la production. Depuis 2019, l’Institut national des métiers d’art pilote la labellisation et la promotion du label EPV au niveau national et international dans le but de faire rayonner les Entreprises du Patrimoine Vivant au travers des valeurs qu’elles véhiculent, des savoir-faire d’exception qu’elles exercent, des dirigeants qui les incarnent et de leur intérêt économique national. Début juillet 2022, le label EPV a signé un partenariat avec les Douanes afin de renforcer les actions communes au service de la protection des entreprises et de la valorisation du savoir-faire français. Trois thématiques sont au cœur de cette convention : le Fabriqué en France ; les accords internationaux ; la protection de la propriété intellectuelle.
Lenzi, labellisée « Entreprise du Patrimoine Vivant »
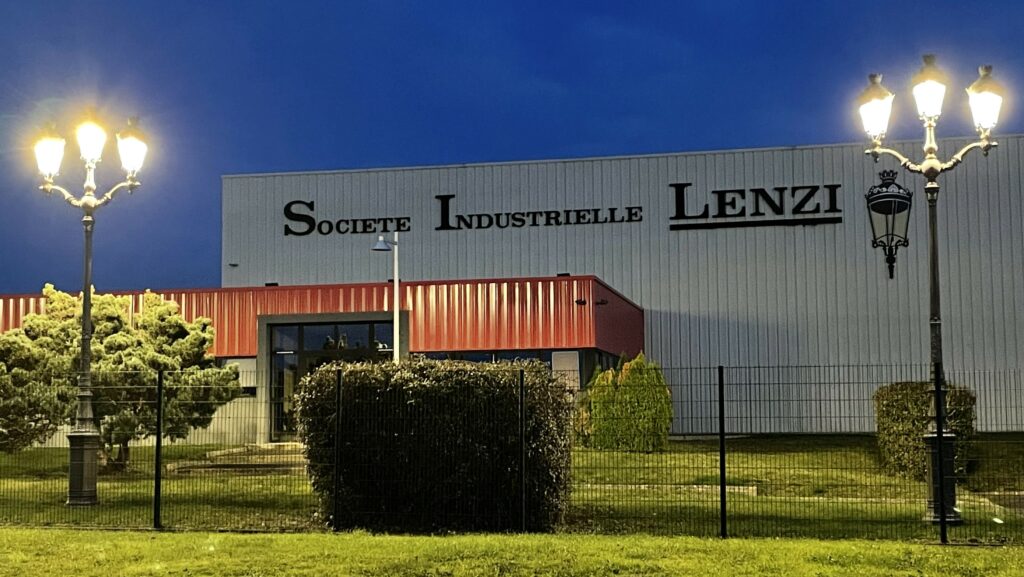
Lenzi a été labellisée EPV la première fois en 2014. La modeste entreprise de chaudronnerie-tôlerie-carrosserie fondée en 1933 à Aulnay-sous-Bois, par Léopold Lenzi, émigré italien, s’oriente vers l’éclairage public 20 ans plus tard, à l’occasion de la grande restauration des sites et monuments de la ville de Paris. Titulaire du marché de remise en état de luminaires anciens sélectionnés par la commission des sites, l’entreprise, qui disposait de spécialistes, devait rapidement fabriquer des « ensembles complets », propres à chaque site : Champs-Élysées, avenue de l’Opéra, rue de Rivoli, butte Montmartre, Place de la Concorde, quartier du Marais, Palais Royal, etc. Dès le départ, une collaboration fructueuse s’était instaurée avec l’Administration des Beaux-Arts et EDF, déterminant les premiers éléments d’une gamme de luminaires qui allait devenir célèbre.
« Tranchant délibérément sur la grande série, conciliant pour la première fois esthétique et technique, ces modèles, adaptés à chaque circonstance, pouvaient enfin résoudre le difficile problème d’intégration harmonieuse du luminaire au cadre environnant, même s’il n’est pas classé, explique Antoine Bonneville, président de Lenzi depuis 2004. Aujourd’hui, notre société est la seule héritière de ce patrimoine unique en France et à l’étranger. Héritière de ces « lanternes de Paris » dont elle a déposé le nom. Depuis 2018, Lenzi complète son offre de produits avec une gamme décorative originale dessinée par des designers. Lenzi est également adhérente à la French Fab ». Lancée le 2 octobre 2017 par le ministre de l’Économie, des Finances et de la Souveraineté industrielle et numérique, la French Fab incarne les entreprises, acteurs économiques, institutions et sites industriels situés en France qui se reconnaissent dans la volonté de développer l’industrie française. « En 2022, nous avons complètement modernisé notre outil de production pour faire davantage du made in France », poursuit Antoine Bonneville.
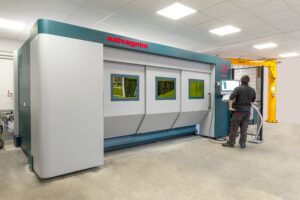
Le site de production est divisé en plusieurs ateliers : – l’atelier de tôlerie : qui comprend une unité de découpe laser dernier cri, et pliage, à commande numérique ; – l’atelier de peinture : avec une chaîne de traitement de surface (sablage et zingage pour les supports), et deux chaînes de thermolaquage, une pour les lanternes et une pour les supports ; – l’atelier d’assemblage où la partie led et l’électronique (y compris pour les lanternes de Paris) sont intégrées ; – l’atelier soudure cintrage dédié aux crosses et consoles ; – l’atelier fabrication : lanternes de fonderie qui nécessitent du perçage, du taraudage, lanternes de ferronnerie, et processus pour les supports ; – l’atelier consacré à la rénovation. « Par exemple, en 2013, la place de la République à Paris a été entièrement refaite et on nous a demandé de rénover les lanternes (100 kg de bronze, 1,20 m de haut), se souvient Antoine Bonneville. On a dû refaire des outillages car il manquait des pièces. Dans ces lanternes, il existe des feuilles qu’on a dû refaire en respectant les plans de l’époque. Nous utilisons aussi bien l’aluminium, le cuivre, l’inox, le laiton, selon nos modèles . Nous sous-traitons tout ce qui est injection plastique, repoussage (formes rondes en ferronnerie), et fonderie, et, à part les pour les leds, nos fournisseurs sont tous français ».
L’arrêté de 2018 a contraint Lenzi à investir dans un laboratoire virtuel qui utilise un logiciel de simulation des flux optiques. « Même si nous avons bénéficié d’un certain nombre d’exonérations, nous devions pouvoir répondre aux exigences de l’arrêté, poursuit Antoine Bonneville. On rentre la conception du produit, sa couleur, la vasque, la puissance, la photométrie, etc. Nous effectuons tous les tests chez nous : d’étanchéité, électriques, sur chaîne. Nous disposons d’un banc de contrôle très sophistiqué qui nous permet d’enregistrer toutes les données de chacun des luminaires. Toutes nos étiquettes disposent d’un QR code qui envoie sur votre smartphone les caractéristiques du produit. À noter que notre bureau d’études travaille sur des produits spéciaux à la demande d’architectes. » Lenzi réalise 25 % de son CA à l’export, dans une cinquantaine de pays et une vingtaine de capitales, y compris Tokyo. « Fabriquer en France est essentiel pour créer des emplois localement et former les jeunes générations », conclut Antoine Bonneville.
Ragni, de l’entreprise artisanale à Groupe Ragni
Comme Lenzi, le fondateur de Ragni, vient aussi d’Italie. L’aventure commence en 1927 avec Victor Ragni, arrière-grand-père de Stéphane Ragni, directeur général associé de Groupe Ragni et de la marque Ragni, qui ouvre son propre atelier de ferronnerie au Cros-de-Cagnes. Des lustres, des appliques, du mobilier et autres pièces décoratives y sont également fabriquées dans l’atelier des Vespins. À la fin des années 1980, Ragni commence à s’atteler à la production de luminaires décoratifs et fonctionnels. « Les agents commerciaux de Clarel, spécialiste de l’éclairage fonctionnel, demandent alors aux frères Ragni (Victor, Roger et Marcel) de lui fabriquer des lanternes de style. C’est ainsi que de ferronniers d’art, nous sommes devenus industriels de l’éclairage, raconte Stéphane Ragni. Nos gammes se sont étoffées en même temps que nous avons ouvert un deuxième site à Tourrettes dans le Var, dédié au traitement de surface et à la peinture des mâts. En 2020, nous avons inauguré près du site industriel historique de Cagnes-sur-Mer dans les Alpes-Maritimes, le nouveau siège social et le centre logistique qui peut abriter jusqu’à 3 500 palettes de stocks de matières premières ».
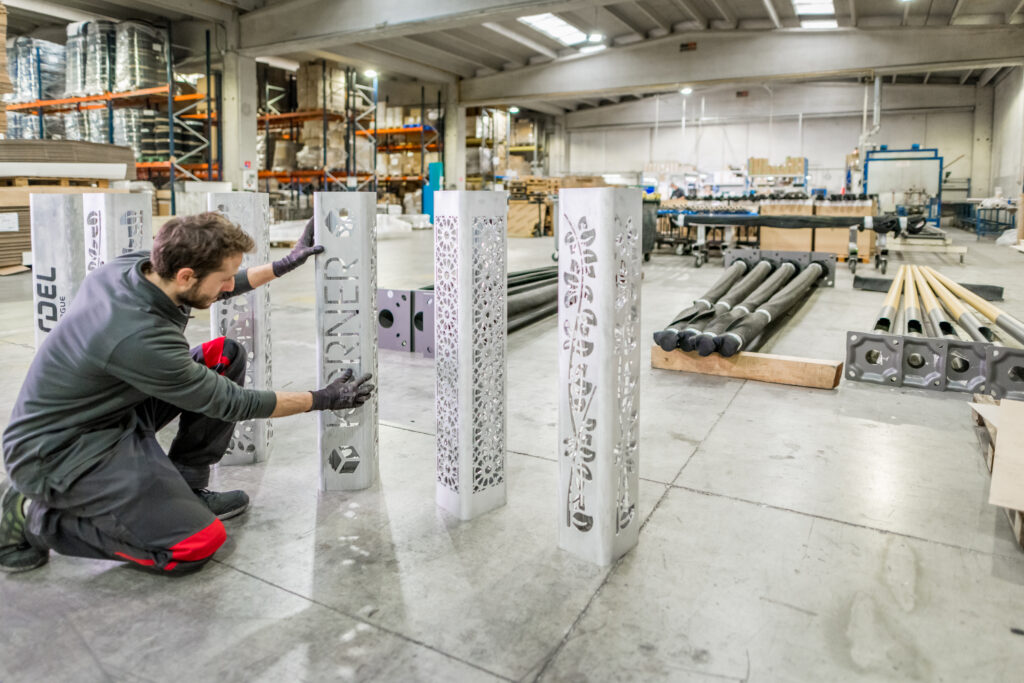
La partie tôlerie regroupe des machines numériques, des robots qui découpent et plient la tôle pour créer les luminaires – de style, les luminaires routiers et contemporains. Puis viennent la peinture et le thermolaquage. Outre les ateliers de montage et d’assemblage, le site dispose également d’un laboratoire de tests, pour la résistance aux chocs (IK) et la protection contre l’humidité (IP). « Ce laboratoire nous fait gagner un temps considérable : ce que nous testons en 24 heures nous prendrait trois semaines à l’extérieur, ajoute Stéphane Ragni.
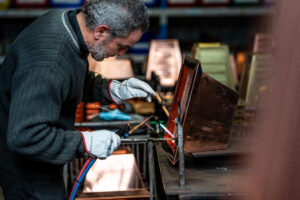
Bien entendu, nos sites de production, de proximité, nous permettent de répondre à du sur-mesure. Déjà, mon oncle et mon père répondaient toujours favorablement à des demandes d’adaptation, c’est ainsi que Ragni s’est développée ! Nous avons reçu, en 2017, le label EPV. Pour nous, cela fait partie de l’histoire de Ragni, car notre savoir-faire s’appuie sur l’histoire des anciens : il se transmet de génération en génération. Et qui dit transmission dit aussi formation, sujet auquel nous réfléchissons sérieusement. Parce que fabriquer en France, c’est œuvrer pour que notre industrie perdure localement. C’est crucial et cela nous tient à cœur ; c’est ce qui a fait qu’on a décidé d’agrandir notre site, sans changer de département. On aurait pu, sans parler de délocaliser à l’étranger, partir des Alpes-Maritimes, et pour le même prix, trouver un terrain quatre fois plus grand dans un autre département. Mais nous avons fait le choix de garder la famille professionnelle. Le message fort que je souhaite faire passer, c’est que nous nous attachons à protéger notre industrie et notre savoir-faire et à redonner de la force à notre pays. Aujourd’hui, Ragni est un des leaders du marché de l’éclairage public en France. Il n’y a pas que la sobriété énergétique qui compte, les collectivités font attention au développement durable et au comportement des fabricants. Nous sommes un des premiers à fournir des PEP (profil environnemental du produit) Ecopassports qui prennent en compte l’ensemble du cycle de vie du produit, de l’extraction des matières premières à sa fin de vie, sans oublier les transports, la mise en œuvre et l’usage même du produit. »
Groupe Ragni comprend aussi, entre autres, Novéa Énergies qui fabrique ses luminaires d’éclairage autonome à Beaucouzé, dans le Maine-et-Loire avec une technologie de batteries développée avec le CEA de Grenoble. « Nous sommes engagés dans le Fabriqué en France et fiers d’avoir conservé notre site dans la région où mon aïeul est arrivé d’Italie, il y a tout juste 100 ans », déclare Stéphane Ragni.
Technilum : plus de 50 ans de techniques et de lumières à la française
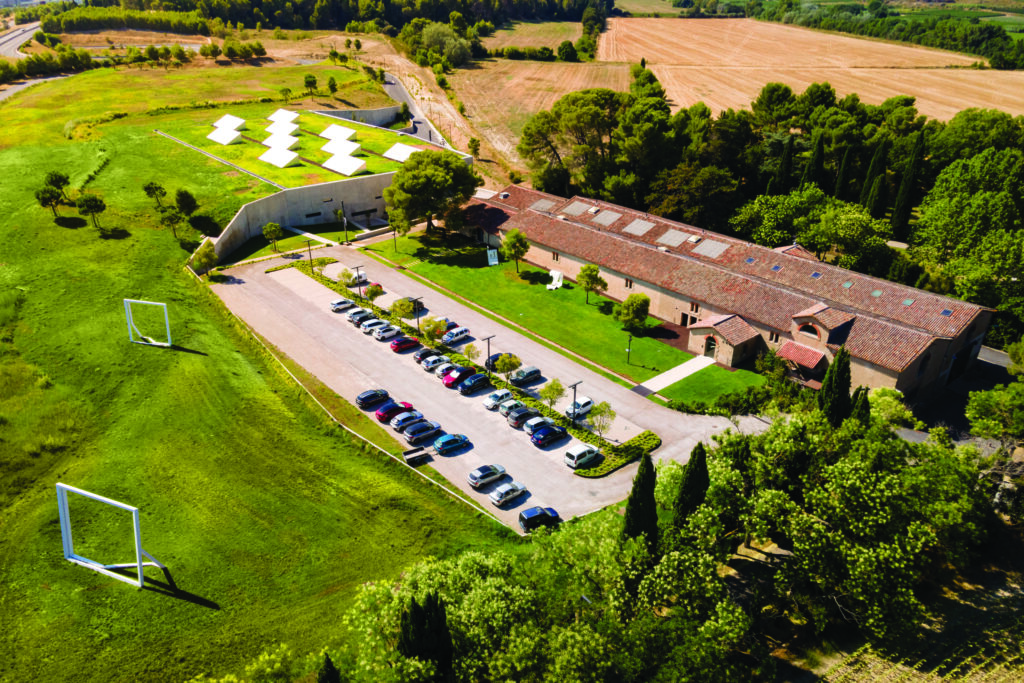
L’entreprise, créée en 1971 à Béziers, par Guy Jullian, au moment de l’aménagement des stations du littoral languedocien, dans le cadre de la mission Racine, se spécialise initialement dans l’éclairage intérieur et extérieur, avec un parti pris pour l’aluminium. « Ce choix a été fait pour des raisons intrinsèques de l’aluminium liées à sa pérennité, la maturité du matériau et sa robustesse, avec les techniques de fabrication de l’époque, restées valables aujourd’hui, à savoir sans soudure », commente Agnès Jullian, présidente de Technilum Group. Tous les assemblages sont sans soudure pour éviter les points de faiblesse et de corrosion sur l’aluminium. Le site de production est resté dans la région de Béziers, à Lézigno, où Technilum s’est installée dans un ancien chai en 1998 auquel a été ajoutée, en 2017, une extension qui a triplé la surface, offrant ainsi de plus grandes capacités de production. « Le site, de plus de 6 000 m², fait partie de l’identité de Technilum, c’est un vecteur de communication, mais aussi d’identité, qui porte les valeurs de l’entreprise, que ce soit en création, innovation et design. Nous fabriquons des luminaires depuis toujours ; ils sont conçus dans la continuité de nos profils, comme Mikado ou Shiraz. Nous développons aussi des gammes de projecteurs. Nos collections nous permettent de couvrir tous les sujets, de l’éclairage décoratif au fonctionnel ».
Les différents ateliers de Lézigno comprennent tous les usinages, qu’il s’agisse des mâts, des luminaires et des composants, tandis que le traitement de surface est externalisé. Puis les produits reviennent à l’usine pour le montage et les tests effectués dans le laboratoire. « Nous ne fabriquons pas à l’avance mais nous proposons une gamme “prête-à-poser”. Notre objectif est de faire du 40 %/60 %, standard /spécifique. Et même le standard chez nous est personnalisable au niveau de la finition, de la hauteur, de la puissance, etc. Nous avons été labellisés EPV en 2017, puis en 2022. Notre certification EcoVadis Or consacre nos engagements RSE. »
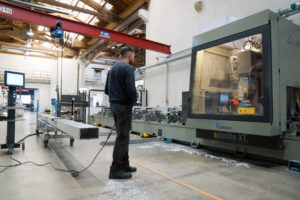
Pour Agnès Jullian, « le principal atout du fabriqué en France c’est la souplesse, l’adaptabilité et le délai. Et, pour la chef d’entreprise que je suis, c’est d’abord une fierté de travailler en France. Et je souhaite que ce soit aussi un métier d’avenir de travailler dans une usine comme la nôtre. Ici pas d’intelligence artificielle, tout passe par l’humain et le travail manuel : c’est important de toucher la matière, de la percevoir, de la sentir, d’avoir la satisfaction de produire sur place, de voir ce que devient le produit, et d’attacher un soin particulier aux matériaux. C’est pour cette raison que nous recrutons beaucoup via l’alternance. Une grosse partie du savoir-faire interne se transmet de personne à personne. Technilum a fait partie des premières entreprises sélectionnées pour la Grande Exposition du Fabriqué en France à l’Élysée en 2020. Nos collectivités doivent encourager le Fabriqué en France. Nombreux sont nos produits qui, installés il y a 50 ans, sont toujours en place, ni rouillés, ni cassés. Prenons l’exemple de la Grande Motte avec Jean Balladur, historiquement, on avait dessiné des luminaires et des lampadaires très spécifiques, qui s’appellent les Fées, installés devant l’hôtel de ville et ils sont toujours en place. Aujourd’hui, on les a refaits, réhabilités, on a changé les luminaires. Ce qui ne nous a pas empêchés de retravailler sur la Grande Motte, en créant un nouveau design très identitaire de la ville. Technilum s’inscrit dans cette démarche comme une entreprise à mission, avec l’agilité qui la caractérise, pour des projets urbains durables, sobres, à faible impact environnemental afin de créer une identité architecturale et urbaine ».
Aubrilam, le travail du bois ancré en Auvergne
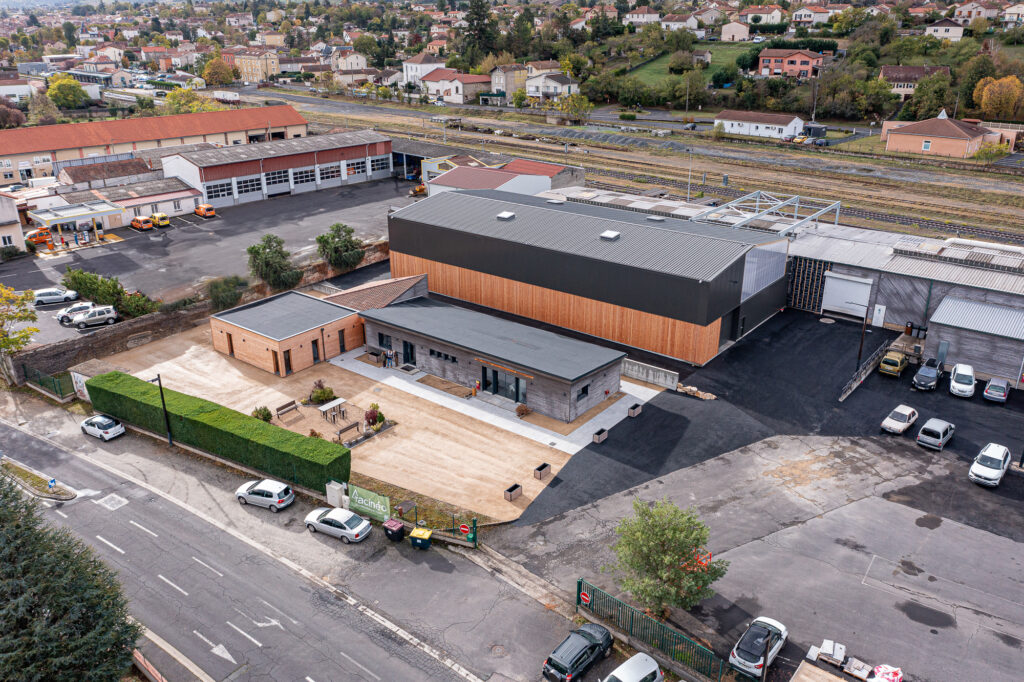
L’entreprise de fabrication de mâts en bois, une ancienne scierie créée vers 1850 qui appartenait à la famille Chambriard à Brioude, a été fondée par Jacques Gouteyron en 1978. Elle est aujourd’hui sous la direction de Soufyane Miloudi (président actionnaire majoritaire d’Aubrilam depuis 2021) au sein du groupe Bega. Aubrilam signifie en fait Auvergne, Brioude et lamellé collé. L’entreprise compte une centaine de personnes réparties sur deux sites : le siège à Clermont-Ferrand avec les fonctions support, commerce, finance, bureau d’études ; et à Brioude le site historique (45 personnes) qui fabrique les mâts et une plateforme logistique (15 personnes) de 2 100 m² ouverte en 2022.
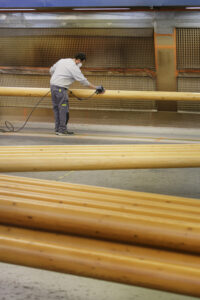
« Environ 5 000 mâts sortent de notre usine chaque année. Le site de production, de 10 000 m², a été agrandi pour y intégrer un nouveau process et une nouvelle machine ainsi qu’un showroom extérieur, explique Lysandre De Pizzol directeur commercial et marketing. Les poutres de lamellé collé de 15,50 m de long, 0,66 m de large et 0,66 m d’épaisseur, arrivent à l’usine pour y être coupées (délignage ou sillage) en 4 planches à l’aide d’une scie à ruban existante que nous avons modernisée pour notre usage. On coupe deux grandes et deux petites planches pour constituer un parallélépipède qui va être passé au banc de collage et soumis à un serrage. Il existe quatre types de mâts : rond droit, rond conique et idem en section carrée. Pour les mâts, on n’utilise que le pin sylvestre lamellé-collé qui vient de Finlande. » Des mesures sont réalisées en laboratoire sur la tenue du collage : il s’agit du test du cisaillement. Le bois étant un matériau vivant, l’usine est contrôlée en permanence en termes d’hygrométrie et de température. À noter que pour les bornes, c’est plutôt le bois Accoya qui est utilisé ; il résulte de la transformation par un procédé d’acétylation de bois durables à croissance rapide. Il en découle un produit particulièrement performant, sain et écologique. Il est imputrescible et très résistant au contact avec l’eau. Il offre les certifications FSC, Cradle to Cradle Certified Gold et a reçu la certification pour la catégorie Material Health (impact sur la santé). Son impact carbone est très faible et il est recyclable à 100 %.
Lors de l’étape suivante, les fûts entrent dans une machine à commande numérique de fraisage à 5 axes qui va effectuer des percements et des épaulements pour venir emboîter les parties métalliques. « Pour les finitions, nous utilisons des lasures 100 % en phase aqueuse, qui ne contiennent pas de solvants, poursuit Lysandre De Pizzol. Ce process permet de mettre en couleur les mâts pour leur donner la teinte choisie, soit en fonction du modèle catalogue, ou pour répondre à une demande spécifique. Nos process nous offrent beaucoup de souplesse, ce qui facilite le sur-mesure de A à Z, du dessin du mât jusqu’à l’assemblage dont la qualité détermine la durabilité des mâts. Plusieurs éléments métalliques peuvent être assemblés selon la demande : l’embase de liaison au sol, l’intégration des leds, des interfaces pour la signalétique, etc. » Aubrilam est certifiée ISO 9001 et ISO 14040 et 14025 pour l’analyse des cycles de vie et les produits ont tous le marquage CE.
Lysandre De Pizzol en convient : « Nous créons des synergies industrielles intéressantes, avec tout un tissu local et des gens avec lesquels on interagit, que ce soient les sous-traitants, les partenaires industriels. Par exemple, pour le nouveau bâtiment, nous avons sollicité une entreprise locale que nous connaissons bien. La transmission du savoir-faire des métiers du bois fait que nous comptons les uns sur les autres : on n’est pas dans un process complètement automatisé où on appuie sur des boutons. Aux côtés des spécialistes de la commande numérique, travaillent des personnes dont les interventions manuelles sur le bois et les connaissances de la matière sont tout aussi indispensables. »
Abel : créativité et réactivité
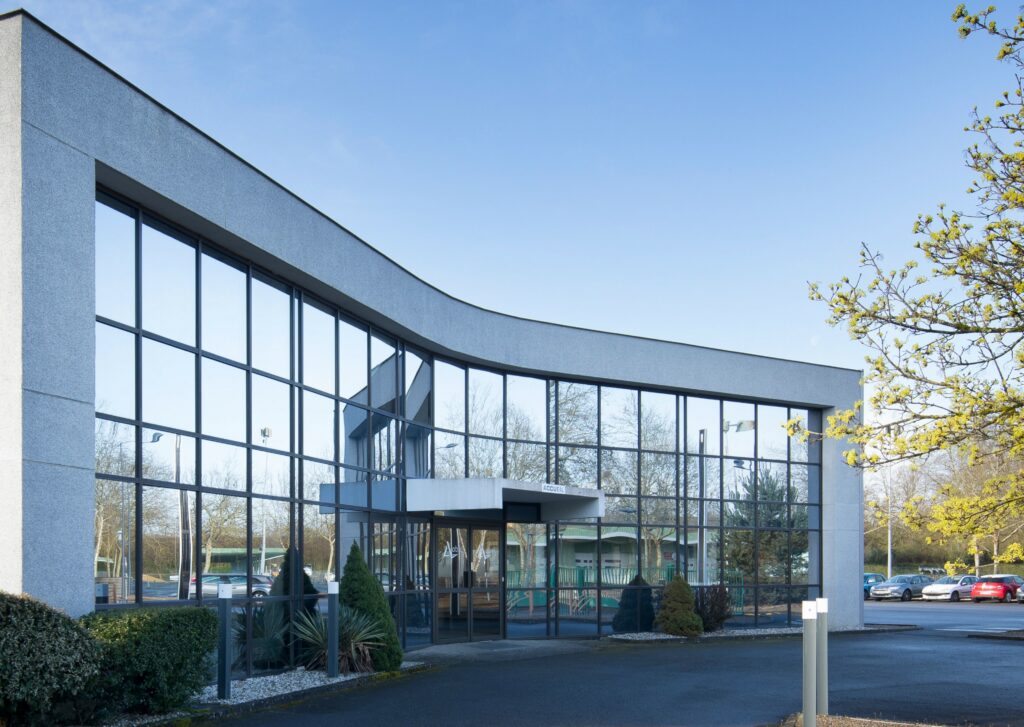
Abel conçoit, fabrique et commercialise des solutions d’éclairage durables, fonctionnelles, décoratives et personnalisables à destination des espaces publics. Créée en 1953 à Brive-la-Gaillarde, en Corrèze, par les frères Fronty – dont certains descendants travaillent encore dans l’entreprise –, Abel commence son activité dans la fabrication de ballasts. Aujourd’hui, elle participe à la rénovation du parc en maîtrisant intégralement et en local ses fabrications et accompagne les communes et les professionnels de l’éclairage dans la modernisation des installations. Les gammes comprennent aussi bien des luminaires à alimentation filaire que solaire, des accessoires de raccordement et de sécurité, des transformateurs pour les réseaux électriques. Entreprise familiale et indépendante, Abel compte 85 salariés ainsi qu’une quinzaine d’agences commerciales partenaires. Son site de production unique est situé depuis 1994 à quelques mètres d’un nœud autoroutier (A20/A89), dans la zone industrielle de Cana.
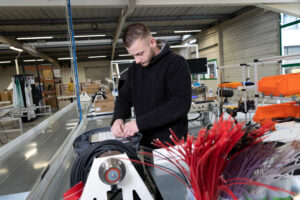
« Abel tient une position stratégique pour ses échanges commerciaux et rayonne sur toute la France, et dans le monde, grâce à ses agences partenaires, commente Denis Pomarel, PDG d’Abel, et privilégie les circuits courts. Sur l’ensemble des composants qui constituent le luminaire 6000-R, plus de 87 % des fournisseurs sont en France dont plus de 50 % en Corrèze. Nos solutions sont adaptées à l’éclairage des rues, routes, places, parkings, promenades, pistes cyclables, aires résidentielles. Nous misons également sur l’éclairage à alimentation solaire pour éclairer partout et simplement, en ayant la possibilité de s’émanciper des réseaux filaires. Ce type d’éclairage s’inscrit dans la transition énergétique en rendant les points lumineux autonomes et axés sur l’autoconsommation. La conception, la fabrication et le montage de la chaîne sont réalisés en interne par nos équipes. 14 ingénieurs travaillent au sein de notre bureau d’études ».
La superficie totale des locaux de Brive-la-Gaillarde est de 13 000 m² dont 6 300 m² sont couverts et 1 000 m² sont dédiés à l’atelier de montage solaire PhotoLight. L’usine est organisée en plusieurs ateliers. L’atelier de tôlerie / mécanique où les feuilles d’aluminium sont coupées et pliées ; une ligne de montage permet de réaliser l’assemblage et le câblage des collections de lanternes dites « runner » avec 6 opérateurs/trices et l’alimentation de la matière première en picking (bord de ligne), et facilite l’acheminement et la préparation des matières premières. Elle apporte aussi un confort ergonomique avec moins de manutention que sur un poste de montage classique. Des ilots permettent d’assembler les lanternes avec des designs un peu plus atypiques et de réaliser le câblage. L’atelier peinture est équipé d’une chaîne automatisée de traitement poudre polyester et d’une cuve d’imprégnation de vernis sous vide. L’atelier bobinage comprend, quant à lui, 4 machines à bobiner numériques et semi-automatiques et une machine à empiler les circuits magnétiques et à les souder. Enfin, une zone protégée contre les effets électrostatiques est destinée au montage des cartes électroniques (drivers et leds). Les tests en brouillard salin, d’étanchéité et de résistance aux chocs mécaniques sont réalisés en interne, au sein du laboratoire.
« Nous pouvons adapter un produit pour répondre à une demande spécifique, cela fait partie de notre savoir-faire, affirme Denis Pomarel. Cela a été le cas pour notre borne S-Pass. Nous avons mené une réflexion commune avec le client pour développer une solution lumineuse novatrice, capable d’offrir une meilleure visibilité côté piéton et côté automobiliste. Nous avons obtenu le Prix de l’innovation au salon des maires et des collectivités locales en 2015-2016. Nous faisons le choix de partenaires responsables et privilégions les circuits d’approvisionnement courts avec des fournisseurs locaux en France et en Europe afin d’optimiser les impacts financiers et environnementaux. Acheter des produits d’éclairage public fabriqués en France est un gage de qualité. Abel consacre plus de 5 % de son chiffre d’affaires à la R&D pour développer des solutions d’éclairage d’aujourd’hui et de demain. C’est un soutien renouvelé à l’industrie et à l’économie françaises. Du bureau d’études aux ateliers, nous maîtrisons totalement nos process pour optimiser notre flexibilité et la gestion de nos coûts. »
Selux : créer sécurité, bien-être et beauté
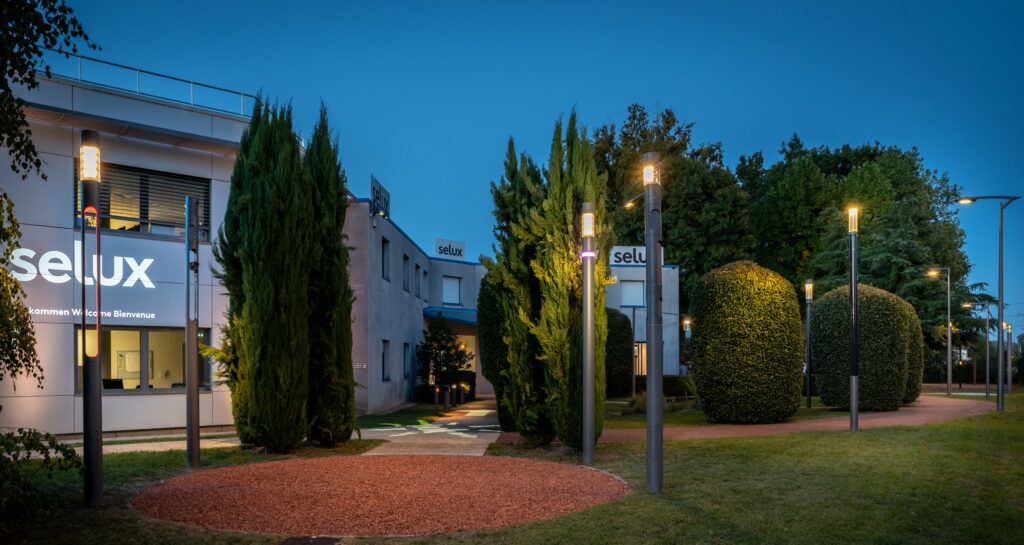
Lorsque Hermann Bansbach fonde son entreprise à Berlin après la Seconde Guerre mondiale, la ville, gravement détruite, est presque sans électricité ni lumière. Bansbach apporte de la lumière dans les moments sombres en facilitant la vie des Berlinois avec un chargeur de batterie. Il estime que la lumière a une signification sociale et culturelle qui va bien au-delà de l’aspect purement économique. La volonté de Selux France est de créer durablement de la valeur pour ses clients, pour l’ensemble de son personnel et pour ses actionnaires, tout en protégeant l’environnement et limitant les consommations des ressources naturelles. C’est en 2014, que la filiale française ouvre ses portes avec un site de production à Miribel au nord-est de Lyon. L’usine actuelle aux Échets emploie environ 65 personnes travaillant principalement sur des luminaires décoratifs et routiers, avec des zones de montage, d’assemblage, de programmation et de stockage.
Selux France est un centre de compétences et un centre industriel pour le groupe. « Au fil des années, l’entreprise française a su s’imposer auprès des interlocuteurs les plus exigeants grâce à sa fiabilité, son sérieux et sa créativité, rappelle Yves Farion, PDG de Selux France. Notre démarche est basée sur la conviction que l’éclairage correspond autant à une attente sociale et culturelle qu’à un besoin purement technique, économique et fonctionnel. Notre philosophie est toujours restée la même : penser global, agir local. La proximité géographique avec les sous-traitants renforce la relation avec les clients, tout en insistant sur une démarche respectueuse de l’environnement. L’entreprise valorise également une approche locale et durable dans toute sa chaîne de production, mettant en avant des équipes dédiées pour assurer un contrôle rigoureux de la qualité. Le site de Miribel assemble 15 000 pièces par an ».
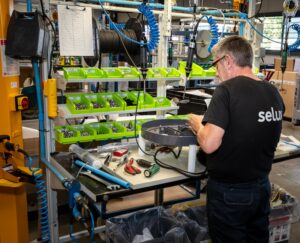
À Brive-La-Gaillarde, les corps des luminaires viennent de fournisseurs, de fondeurs de la région, ou d’Italie, du Portugal, d’Allemagne bien sûr, toujours d’Europe. Les platines led sont placées à l’intérieur de la tête de luminaire, puis vient se fixer le verre trempé, issu d’un fournisseur allemand, et les câbles (entre 5 m et 10 m) sont connectés. Le site de Miribel, outre les zones d’assemblage et de montage, qui couvrent une surface de 1 400 m², intègre une plateforme logistique, avec une zone de réception et d’expédition de 800 m². Selux France s’est organisé en processus orientés clients avec des objectifs, des indicateurs, et des plans d’actions gérés par les pilotes en cohérence avec les priorités définies et suivis régulièrement afin d’en évaluer l’efficacité.« Nos priorités et les objectifs associés sont revus annuellement, afin d’être en adéquation permanente avec les attentes des clients, le contexte économique, les évolutions normatives et notre budget, ajoute Yves Farion. Le responsable Qualité Environnement est un support aux pilotes de processus, pour mettre en œuvre et surveiller le fonctionnement de notre système, qui intègre les exigences concernant le marquage CE et la sécurité électrique des produits. Selux met régulièrement en place des actions visant à engager l’ensemble de ses parties prenantes dans une démarche responsable sur le long terme. À ce titre, nos certifications ISO9001 (Qualité, depuis 2002) et ISO14001 (Environnement, depuis 2011) permettent de fixer un cadre de travail et d’organisation. » Depuis 2022 Selux est membre de la communauté du Coq Vert, qui regroupe des entreprises engagées dans la transition écologique et énergétique.