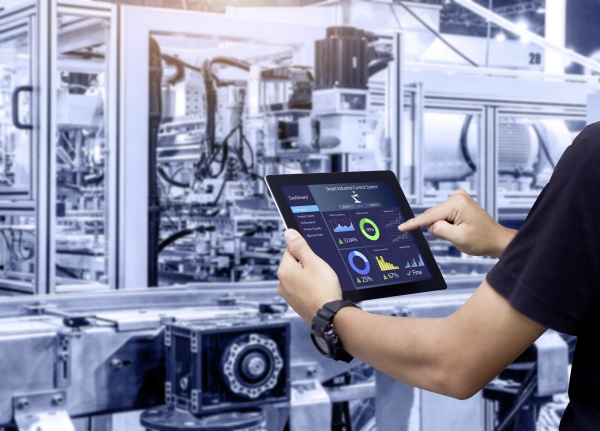
L’Industrie 4.0 va permettre d’augmenter la productivité, de réduire les coûts, d’améliorer la flexibilité de l’usine du futur. Cela doit aussi passer par plusieurs transitions : numérique, écologique et sociétale. La maîtrise des consommations énergétiques va bénéficier des technologies numériques et de la digitalisation de tous les secteurs industriels pour gagner en compétitivité. Une évolution qui ne va pas concerner que la grande industrie, mais peut aussi être mise en œuvre dans les PME/PMI avec des retours sur investissement rapides.
Le concept de l’Industrie 4.0, apparu il y a une dizaine d’années en Allemagne, est aujourd’hui devenu incontournable dans tous les secteurs de l’industrie, avec un ensemble de solutions numériques pour rendre les moyens de production connectés et communicants, mais aussi flexibles et économes en matières et en énergie. Deux études portées par l’ADEME illustrent l’émergence de ces questionnements : grâce au dynamisme des transitions énergétique et numérique, l’industrie remet en cause ses schémas classiques (manière de produire, de concevoir, d’innover). Toutefois, l’aspect environnemental de l’innovation numérique, qui reste très énergivore et consommatrice de ressources, reste un paramètre clé encore peu étudié, note l’ADEME.
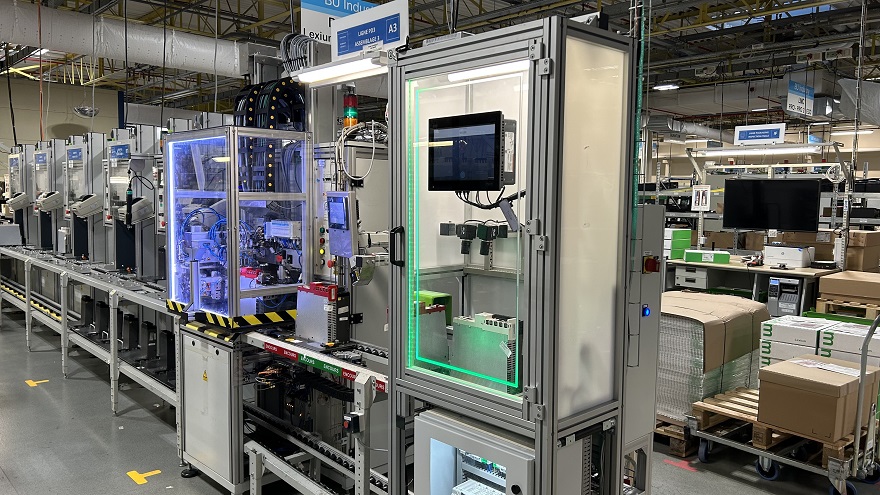
L’arrivée à maturité de nouvelles technologies, d’outils, de l’Internet industriel des Objets (IIoT) ou d’algorithmes (Big data, cloud et Edge Computing, robots et cobots, jumeaux numériques, impression 3D ou 5G) va permettre d’effectuer cette transition énergétique et écologique.
Si l’Industrie 4.0 doit permettre aux entreprises d’améliorer la productivité et la qualité des produits, d’assurer la continuité d’exploitation, de réduire les temps d’arrêt des équipements et d’optimiser les investissements, elle doit aussi permettre de réduire les consommations d’énergie et les émissions de carbone, de mieux adapter les modes de production à la disponibilité et aux coûts variables des énergies.
Objectifs 2030 et 2050 : consommer moins pour produire mieux
Les nouvelles technologies et la transformation numérique qui prennent une place de plus en plus importante dans l’atelier ou l’usine 4.0 vont avoir un impact positif sur les enjeux environnementaux et les objectifs dictés par les nouvelles réglementations telles que la Stratégie nationale bas-carbone (SNBC).
D’après le rapport gouvernemental de mars 2020 pour la « Transition écologique et solidaire vers la neutralité carbone », qui définit la SNBC de l’industrie à l’horizon 2030 et 2050, l’industrie représente 17,4 % des émissions de gaz à effet de serre de la France. Ces émissions sont dues à la combustion d’énergie nécessaire à la production industrielle (64 %) et aux procédés industriels proprement dits (36 %). La stratégie vise une réduction de 35 % des émissions du secteur par rapport à 2015 et de 81 % à l’horizon 2050.
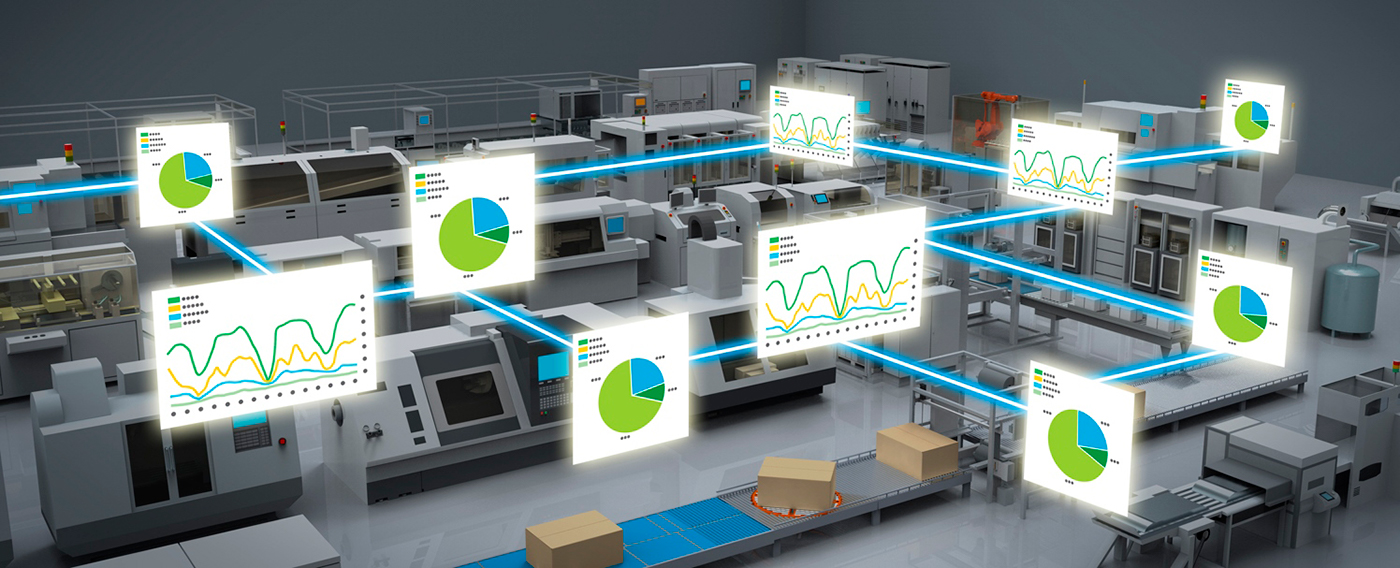
Selon Bruno Duval, responsable Marketing Sud Europe de Sphinx, société spécialisée depuis 22 ans dans la mise en réseau d’équipements industriels et de capteurs, « l’application de l’Industrie 4.0 peut contribuer à améliorer l’efficacité énergétique dans le secteur industriel de plusieurs façons.
- Collecte et analyse des données en temps réel de la consommation d’énergie des équipements et des machines. Cela permet d’identifier les inefficacités et de prendre des mesures correctives pour optimiser les processus et réduire la consommation d’énergie.
- Automatisation et contrôle intelligent : l’Industrie 4.0 favorise l’automatisation des opérations industrielles, ce qui peut contribuer à une utilisation plus efficace de l’énergie. Les systèmes de contrôle intelligents peuvent ajuster automatiquement les paramètres de fonctionnement des machines et des systèmes en fonction des besoins réels, ce qui évite les gaspillages d’énergie liés à une surproduction ou à des équipements inactifs.
- Optimisation de la chaîne d’approvisionnement : l’Industrie 4.0 facilite la connectivité entre les différents acteurs de la chaîne d’approvisionnement, ce qui permet d’optimiser la planification, la logistique et les opérations. Une meilleure coordination réduit les délais d’attente, les temps d’arrêt et les inefficacités, ce qui se traduit par une consommation d’énergie plus efficace dans l’ensemble du processus de production.
- Utilisation des énergies renouvelables : l’Industrie 4.0 peut faciliter l’intégration des sources d’énergie renouvelable, telles que les énergies solaire et éolienne, dans les processus de production. Les systèmes intelligents peuvent prendre en compte les variations de disponibilité de ces sources d’énergie et ajuster la consommation en conséquence, ce qui permet de maximiser l’utilisation des énergies renouvelables et de réduire la dépendance aux combustibles fossiles. Il faut pour cela mettre en place une infrastructure réseau résiliente ».
La digitalisation des process et installations comme leviers d’économies d’énergie
La première étape sera le recueil de données ; des données recueillies par des capteurs sur les différents actifs physiques de l’entreprise, transmises à l’aide de l’Internet industriel des Objets, analysées et comparées à des modèles prédictifs.
L’objectif sera la détection de processus inefficaces, des équipements défectueux ou mal adaptés, des consommations inutiles. Cela doit aussi permettre d’optimiser la maintenance des équipements, la logistique, le chauffage/ventilation/climatisation des bâtiments.
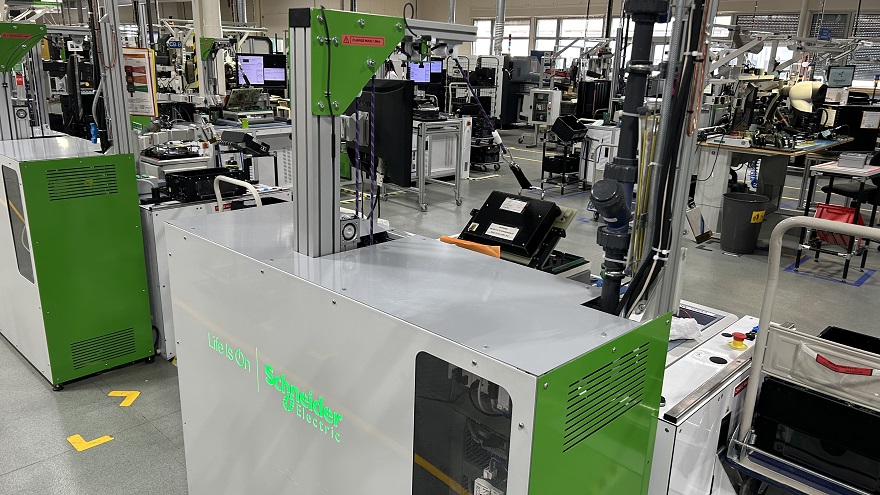
Et comme le souligne Aurélien Fanget, directeur Marketing Industrial Automation de Schneider Electric France : « La transformation digitale n’est pas un objectif, c’est un moyen pour devenir plus efficace et cela commence par un audit afin de comprendre l’état des lieux pour évaluer les besoins de l’entreprise. Ensuite, il convient de définir les objectifs : quels sont les besoins de l’entreprise en matière d’efficacité énergétique et définir les indicateurs de performance liés à ces objectifs. C’est cette phase d’audit qui permet de construire un programme avec l’entreprise. Schneider Electric intervient dès cette phase d’audit et jusqu’à la construction du programme, ce que nous avons appliqué à nos usines, car nous sommes également un industriel : nous avons 200 usines dans le monde, dont 23 en France ».
Pour Quentin Ohran, chef de produit Automation de Wago France, il est difficile d’envisager une amélioration sans mesure : « Une démarche similaire à l’optimisation énergétique des bâtiments doit être appliquée, en allant plus loin dans l’analyse et en ciblant tout d’abord les procédés les plus énergivores de chaque machine et de chaque système. On ne collectera pas uniquement les données énergétiques, mais également les indicateurs de production : c’est la corrélation des deux qui permettra l’optimisation de l’efficacité énergétique. Il faut donc mettre en place des solutions de mesure de l’énergie aux postes stratégiques via des équipements dédiés. Pour la collecte des données de production, deux cas de figure se présentent : pour les nouvelles installations, la collecte et la remontée native des indicateurs. Pour les usines existantes qui passent par l’étape de digitalisation, la collecte des données peut se faire par le biais des bus de terrain déjà en place (Modbus, protocole S7…) et/ou par l’installation de nouveaux capteurs.
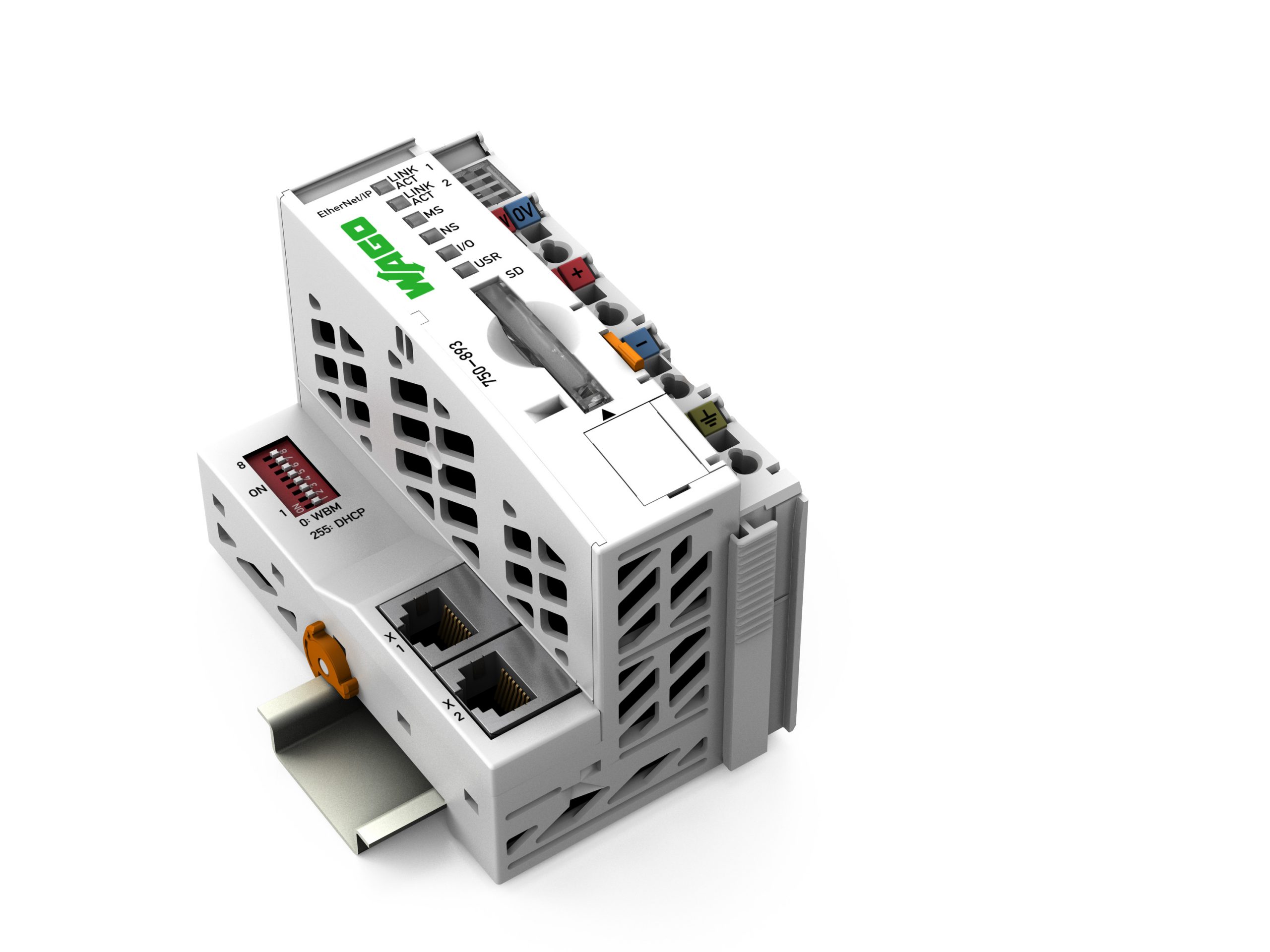
Au-delà de la collecte et de l’analyse, il faudra appliquer le pilotage énergétique au cas par cas. En dehors de la performance énergétique, il est possible d’aller plus loin pour les plus gros consommateurs, jusqu’à introduire l’effacement électrique lors de pics de consommation. Il faudra pour cela que le pilotage énergétique s’interface avec la plateforme de RTE ou, le cas échéant, l’agrégateur d’effacement.
Le premier maillon de la connectivité se trouve évidemment au niveau des capteurs et actionneurs, au plus près de la machine. Le standard IO-Link dont les avantages ne sont plus à présenter offre un accès à de nombreuses données de process et même à la configuration et la calibration du capteur. L’automate qui assure le pilotage du process a un rôle central. Celui-ci doit pouvoir assurer une connexion distante en toute sécurité. Le recours à des technologies ouvertes et standardisées est crucial pour garantir l’interopérabilité sur toute la durée de vie de l’installation. MQTT est le protocole idéal pour cela : léger, sécurisé selon les derniers standards de sécurité, et supporté par de nombreuses solutions SCADA ou cloud.
Il est impératif que cette possibilité de connexion n’introduise aucune vulnérabilité sur la machine ou l’installation : un panel de mesures de cybersécurité doit être proposé nativement sur l’équipement. La suite logicielle assurant la collecte, le traitement, le stockage et l’analyse des données peut être hébergée sur un serveur distant, dans le cloud, on parle alors de Cloud Computing. Il est également possible que cette tâche soit assurée par des équipements dédiés, sur site, on parle alors de Edge Computing. »
Des solutions pour transmettre les informations des capteurs ou compteurs d’énergie ou d’environnement physique
Collecter et transmettre les nombreuses données de l’usine 4.0 est la première étape avant leur analyse et traitement. Bruno Duval donne l’exemple pour la relève des compteurs de fluides ou d’énergie du passage du relevé manuel au passage à la télérelève avec des capteurs autonomes sans fil sur réseau LoRaWAN : « La première solution pour connaître ses consommations est de faire des relevés in situ. Cette tâche peut être longue et fastidieuse si le nombre de compteurs est élevé ou si le site est vaste. Cette méthode est aussi source d’erreurs si le relevé se fait manuellement sur une feuille volante. Par ailleurs, le site utilise peut-être de hautes tensions électriques, ou comprend des zones avec du gaz type ATEX. Des autorisations spécifiques sont alors exigées, ce qui rend la tâche plus complexe. Bref, un relevé manuel des compteurs devient vite contraignant et chronophage.
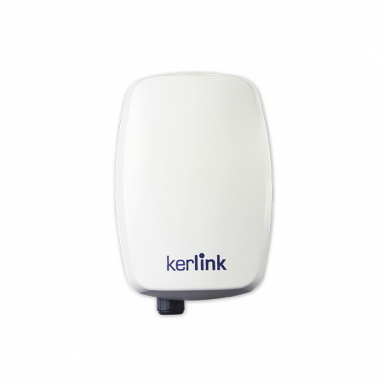
La deuxième solution pour relever ses compteurs peut être d’utiliser un système câblé. En effet, bon nombre de compteurs ou sous-compteurs sont communicants (impulsions, Modbus…) ; ils peuvent alors interagir avec des automates ou une supervision. Si le réseau filaire ou les automates sont à proximité, le câblage est envisageable. Vous pouvez alors réaliser l’opération à peu de frais.
En revanche, si un câblage important est à prévoir, le montant à investir sera élevé. Le retour sur investissement devient défavorable, d’autant plus que l’information n’est pas cruciale dans le processus de fabrication. La troisième solution associe des objets connectés (IIoT) et des passerelles LoRaWAN. Cette solution sans fil, rapide à installer et économique, permet de télérelever tous les compteurs très régulièrement sans risque d’erreur. L’architecture du système comprend une ou plusieurs antennes pour couvrir le site et des capteurs sans fil (sur piles). Ces capteurs, ou objets connectés, permettent de récupérer et remonter les index de compteurs. Les capteurs, ou objets connectés, sont en veille la majorité du temps ; ils se réveillent uniquement à intervalle régulier, le temps de remonter les valeurs. Ce fonctionnement permet aux piles qui les alimentent de durer cinq ans ou plus ; la maintenance du système est donc très limitée. La ou les antennes réceptrices sont connectées à la supervision ou à une plateforme dans le cloud pour mettre en lumière les consommations.
Une passerelle LoRaWAN peut raccorder jusqu’à 1 000 capteurs sans fil (par exemple des capteurs Watteco fabriqués en France) à un système SCADA, une GTB ou à une plateforme de visualisation des données dans le cloud. Une passerelle Kerlink, fabriquée en France et utilisée par des opérateurs comme Orange pour leur réseau LoRaWAN, peut aussi être mise en place pour créer un réseau privé (donc dispensé d’abonnement) ».
Quelles solutions pour une meilleure connexion des machines et des installations via l’IoT ?
Quentin Ohran donne l’exemple des solutions proposées par Wago : « Le système d’entrées/sorties WAGO-I/O System 750 assure le process en lui-même (grâce à sa modularité et ses 500 cartes d’E/S), mais également la collecte des consommations énergétiques par le biais de cartes de mesure dédiées. Ces modules de mesure de puissance à l’encombrement très réduit assurent la collecte de nombreuses grandeurs physiques (courant, tension, puissance et énergie active, réactive, apparente, facteur de puissance, harmoniques…) d’un réseau triphasé ou de 3 réseaux monophasés.
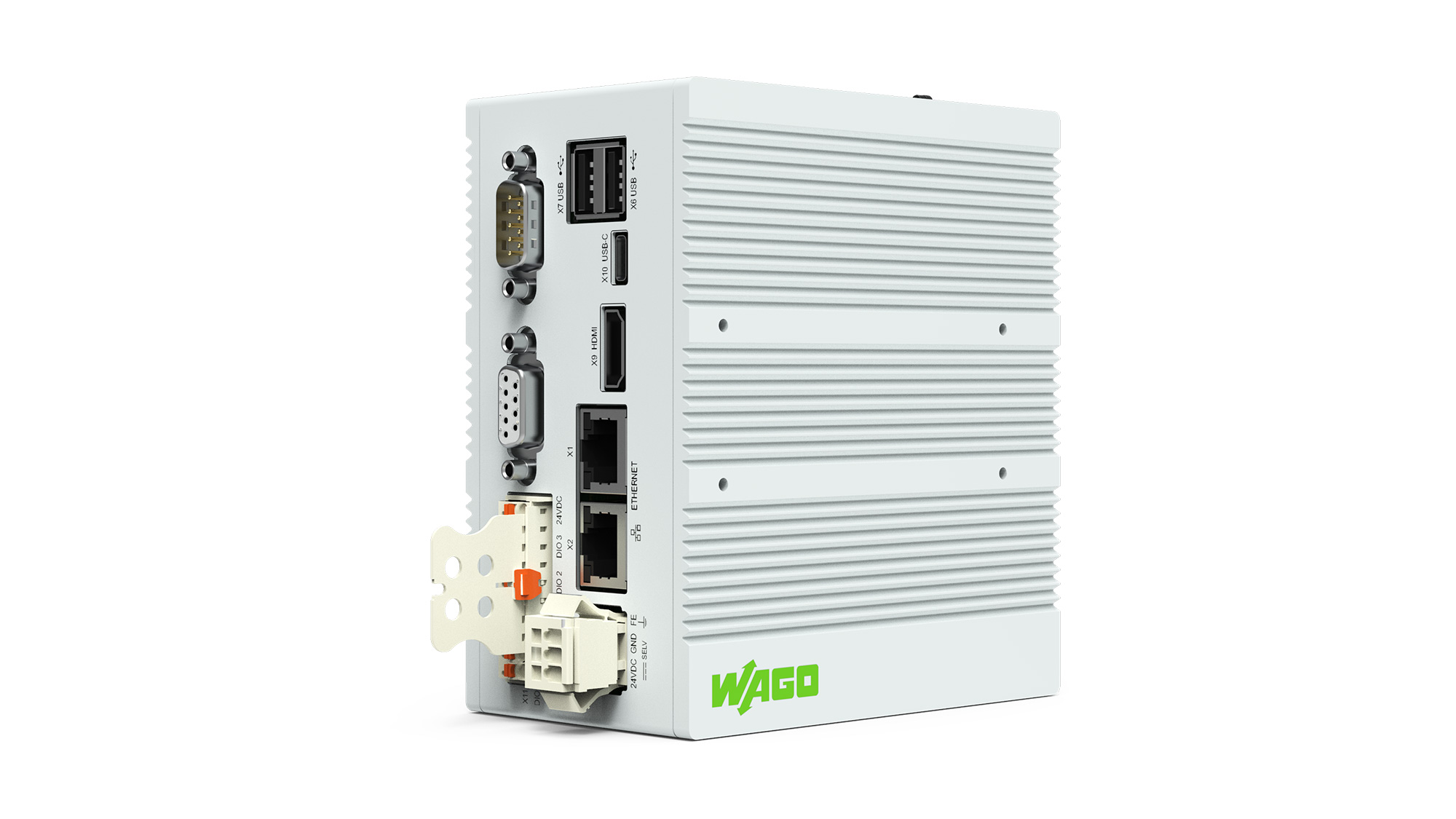
Pour une installation au plus près du terrain et dans les conditions les plus difficiles, le système d’entrée/sortie IP67 WAGO-I/O System Field offre la possibilité de connexion de capteurs/actionneurs TOR ou IO-Link, et supporte les protocoles standard du marché : Profinet, EtherNet/IP et EtherCAT. Les modules d’E/S supportent même la remontée de données directement en MQTT.
La connectivité cloud des contrôleurs Wago, qui se base sur le protocole MQTT, est compatible avec toutes les plateformes cloud du marché. Les données collectées peuvent être transmises à une plateforme cloud généraliste, mais Wago propose également une solution cloud prête à l’emploi : le WAGO Cloud. Cette solution offre une vue d’ensemble des différents équipements et sites, des tableaux de bord personnalisables et un gestionnaire d’alarme intégré. Une approche Edge Computing est également proposée ; dans ce cas, des équipements conçus pour les tâches de collecte, traitement et d’analyse des données sont proposés : les Edge Computers. Des solutions 100 % open source peuvent y être déployées facilement pour tous les aspects de ce traitement d’information, grâce au support de la technologie de conteneurisation Docker. »
Willy Mulot, chef de produit Automatisme et Réseau de Phoenix Contact France, complète : « Pour éviter le gaspillage énergétique, des solutions connectées dites “intelligentes” permettent d’avoir des informations en temps réel. Ainsi, vous identifiez les économies d’énergie potentielles et vous mettez en place les actions nécessaires. Forte de son expertise dans le milieu industriel, Phoenix Contact conçoit des solutions parfaitement adaptées aux environnements humides, poussiéreux et extrêmes. Selon les gammes, nous proposons des plages de températures étendues, jusqu’à l’IP67, ATEX et IK10. [Schéma 2] Pour disposer des données de n’importe où et 24 h/24, il faut avant tout remonter les informations du terrain, et pour cela, une communication fiable s’impose. Avec les entrées et sorties de Phoenix Contact, la détection des signaux d’entrées et de sorties se fait directement dans l’armoire électrique ou de manière déportée. Avec un IP65/67, la nouvelle génération d’E/S Axioline E permet une automatisation décentralisée hors de l’armoire pour une utilisation directe dans une machine et des conditions ambiantes hostiles. De plus, leur résistance particulière aux perturbations CEM et leur robustesse mécanique permettent de minimiser avec ces appareils les temps d’arrêt de l’installation. »
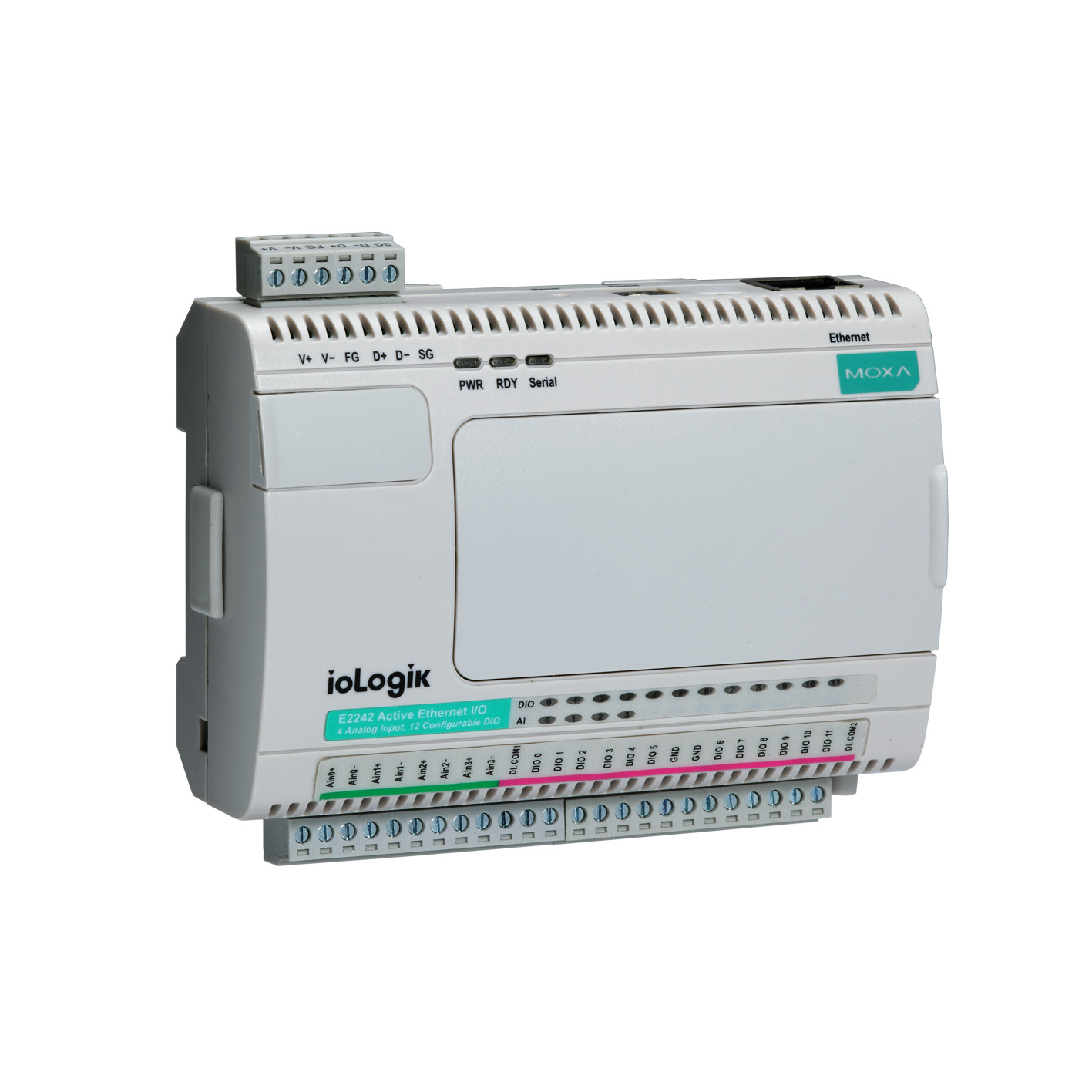
Christian Amat, directeur commercial d’ADM21, distributeur spécialisé dans la fourniture de produits de communication et Ethernet durcis, explique comment des solutions Moxa permettent une efficacité énergétique active avec un minimum d’efforts de programmation : « En déployant des capteurs de détecteur de température à résistance (RTD), des wattmètres et des E/S à distance Ethernet dans l’environnement physique, des données série, numériques et analogiques en temps réel sur la température ambiante, la température du refroidisseur refroidi à l’eau, la vitesse de la pompe et la consommation d’énergie peuvent être acquises et transmises à la base de données pour déterminer une action ultérieure. Pour activer automatiquement le réglage des paramètres du refroidisseur, de la pompe et du ventilateur en fonction de la température en temps réel dans le bâtiment, les commandes permettant de réguler le fonctionnement du CVC intelligent peuvent être définies par Click&Go Plus, une logique de contrôle sans programmation incluse dans les E/S distantes Ethernet (ioLogik Series). Les canaux DI surveillent l’état de la machine du refroidisseur, de la pompe et du ventilateur. Les canaux DO contrôlent les paramètres du refroidisseur, de la pompe et du ventilateur en fonction des informations fournies par les E/S à distance Ethernet (ioLogik E1260), qui prend des lectures de température autour du bâtiment. »
La notion de cybersécurité ne doit pas être oubliée dans le traitement des données
« Une fois récoltées, les nombreuses données doivent être traitées afin de les rendre exploitables. Pour cela, il est important de travailler avec des langages de programmation (C++, C#, Python…), sur un système d’exploitation Open source Linux, note Willy Mulot, de Phoenix Contact. Ainsi, la programmation se fait en langage évolué et en conformité avec la norme IEC 61131-3. En effet, il ne faut pas oublier la notion de cybersécurité. C’est pourquoi Phoenix Contact est le premier fabricant à recevoir la certification d’un automate selon la norme CEI 62443-4-1 ML 3 Full Process Profile, en combinaison avec la norme CEI 62443-4-2. Quoi de mieux que des solutions ouvertes, flexibles, configurables, compactes et pouvant être utilisées pour la commande, le diagnostic et la surveillance de capteurs et machines ? La technologie PLCnext est le lien interopérable (multiprotocole) entre les mondes IT et OT (exemple OPC UA, MQTT). Ce peuvent être des alarmes lors de températures ou de vibrations élevées, des tableaux de bord avec des indicateurs clés de coûts tels que les coûts d’énergie/de matières premières/de stockage, des cartes thermiques de l’usine montrant les zones de l’usine où la consommation d’énergie est élevée, des graphiques montrant les tendances des prix des matières premières utilisées pour la production et des tableaux financiers… Pour cela, utilisez les PC industriels de dernière génération qui sont ultracompacts et robustes avec la technologie CPU actuelle (Elkhart Lake) : les box PC Valueline 3. ».
« Les automates Wago, programmables via l’outil d’ingénierie gratuit et multiconstructeur CODESYS, transmettent les données de façon sécurisée pour traitement et stockage, précise Quentin Ohran. Ces derniers bénéficient de nombreuses fonctionnalités de cybersécurité natives : pare-feu configurable, authentification 802.1x, tunnel VPN, journalisation syslog… »
Quelle place pour les robots dans l’industrie 4.0 ?
De nombreuses entreprises adoptent des innovations technologiques telles que les robots, cobots (robots collaboratifs) ou AMR (robots mobiles autonomes) pour réduire le nombre de tâches manuelles répétitives ou dangereuses de leurs salariés, adapter la flexibilité de leur fabrication et augmenter la productivité. Mais ces solutions d’automatisation ont aussi un intérêt, qui n’est pas toujours très visible, pour améliorer l’efficacité énergétique d’un process ou d’une ligne de fabrication.
Dans une enquête mondiale menée par ABB auprès de 1650 grandes et petites entreprises en Europe, aux États-Unis et en Chine, 84 % des entreprises ont déclaré qu’elles utiliseraient davantage la robotique et l’automatisation au cours de la prochaine décennie, tandis que 85 % ont déclaré que la pandémie avait « changé la donne » pour leur entreprise et leur industrie ; la pandémie de Covid-19 étant un déclencheur pour l’accélération des investissements dans l’automatisation.
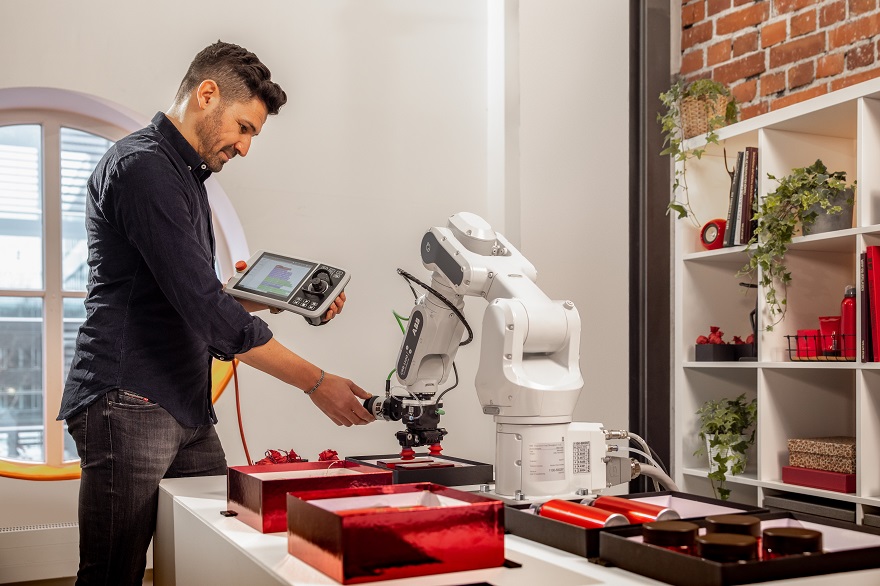
Avec les cobots GoFa™ et SWIFTI™, ABB a élargi son portefeuille de robots collaboratifs. Ces derniers offrent des charges utiles, des vitesses plus élevées et complètent les familles de cobots ABB YuMi et YuMi monobras. « Encore plus puissants, plus rapides et plus performants, ils accélèrent l’expansion de l’entreprise dans des segments à forte croissance tels que l’électronique, la santé, les biens de consommation, la logistique et l’agroalimentaire. »
Comme le souligne Aurélien Fanget, de Schneider Electric, « la robotique est aussi un enjeu de souveraineté afin d’avoir une industrie performante, agile et efficace. D’après des chiffres de l’International Federation of Robotics, en 2016 la France occupait le 18e rang mondial de la robotisation avec 132 robots pour 10 000 employés ; en 2021, on est passé à 163, mais aussi au 20e rang mondial. On doit donc accélérer sur la robotique, car elle permet l’efficacité opérationnelle. Ce développement va faire évoluer les métiers, car les solutions comme le robot collaboratif (cobot) permettent de décharger l’opérateur des tâches répétitives et lourdes, qui va se concentrer sur des tâches à valeur ajoutée. Schneider Electric a une offre Lexium MC12, un multi-chariot pour le transport, le regroupement et le positionnement des produits dans des processus industriels. Associé à la technologie de jumeau numérique, le nouveau système multi-chariot répond aux besoins croissants d’agilité et de commercialisation rapide des machines de production. Cette solution peut être combinée avec notre solution de Robot Delta, pour des opérations de palettisation, par exemple ».
« En utilisant EcoStruxure Machine de Schneider Electric, dont le système Lexium MC12 multi-chariot, nous pouvons intégrer nos opérations beaucoup plus facilement. Nos machines seront plus rapides, plus modulaires et moins encombrantes, ce qui nous permettra de réduire nos coûts de 30 à 40 % et d’effectuer des changements de production jusqu’à 50 % plus rapides. Nous pourrons également mieux servir nos clients leaders dans le secteur agroalimentaire avec une maintenance plus simple, assurée par une solution numérique à hautes performances », déclare Federico Scornaienchi, responsable export chez Livetec.
Jocelyn Peynet, directeur France d’Universal Robots, renchérit : « Parmi les principaux objectifs de développement durable que la cobotique permet d’atteindre, la réduction des déchets, la consommation d’énergie modérée et l’optimisation des surfaces de production sont les plus tangibles. En ce qui concerne les matières premières, l’un des moyens les plus efficaces de réduire le gaspillage est d’améliorer la qualité des procédés de fabrication. Non seulement les cobots Universal Robots sont fabriqués selon des normes de qualité élevées, mais ils sont également des outils éprouvés pour réduire les consommations et les déchets. Avec la cobotique, il est possible d’augmenter l’efficacité d’un large éventail de processus de fabrication, allant de l’usinage (ou le façonnage) à l’assemblage, en passant par le collage et la finition. [Photo 12] Les robots traditionnels sont très souvent démesurés en taille et en masse par rapport à la charge utile qu’ils manipulent. Une très grande part de l’énergie consommée est donc principalement utilisée pour faire se déplacer le robot seul. Le cobot est conçu et optimisé pour être le plus léger et compact possible tout en lui permettant d’automatiser la plupart des tâches réalisées manuellement. Le ratio masse cobot/masse de la charge utile manipulée est donc largement inférieur aux solutions d’automatisation traditionnelles. En résulte une consommation énergétique optimisée et minimisée. À titre d’illustration, la puissance moyenne d’un UR3e est de seulement 100 W, équivalente à celle d’un ordinateur de bureau.
Une fois les cobots déployés, il est en outre possible de s’assurer qu’ils sont utilisés à leur plein potentiel tout en évitant le gaspillage d’énergie. L’écosystème UR+ propose une large gamme de solutions de télésurveillance qui permettent aux utilisateurs d’optimiser les performances de leurs cobots sans avoir à intervenir directement sur la cellule. »
Des solutions et plateformes numériques pour collecter et analyser les données
ABB propose une gestion intégrée des énergies et des équipements électrique moyenne et basse tension sous forme d’un service logiciel (SaaS). Jean-Baptiste Dumanois, Marketing Development Manager d’ABB France, présente cette solution : « AbilityTM Energy and Asset Manager fournit un service de gestion des équipements et de l’énergie adapté aux applications spécifiques des exploitants. Les utilisateurs peuvent afficher et analyser les données sur les performances des installations et gérer les équipements pour optimiser la consommation d’énergie en temps réel et améliorer l’efficacité globale du site. Avec un accès instantané, à tout moment et en tout lieu, la solution convient aux sites industriels et infrastructures de taille intermédiaire et fait économiser aux clients jusqu’à 30% sur leurs factures d’énergie et jusqu’à 40% sur les coûts de maintenance. ABB AbilityTM Energy Manager va permettre de visualiser les données d’une usine avec des tableaux de bord préconfigurés et personnalisables, d’obtenir des rapports Excel et PDF planifiés avec des informations pertinentes sur le site et dans le cadre d’audits énergétiques de garder les consommations sous contrôle, d’améliorer l’efficacité et de surveiller les indicateurs de performance énergétique.
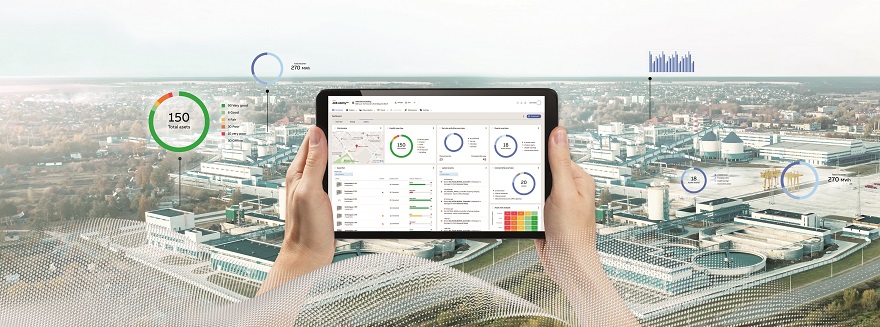
Pour réduire les coûts énergétiques, améliorer l’efficacité énergétique et gérer l’empreinte carbone dans le secteur industriel, il est nécessaire de mettre en place des mesures et des objectifs clairs afin de parvenir à une amélioration continue. Dans ce contexte, l’offre ABB AbilityTM Energy Manager s’enrichit de nouvelles éditions venant ajouter des possibilités additionnelles à l’édition Watching déjà existante.
L’édition Performing a été spécialement conçue pour prendre en compte les facteurs qui peuvent avoir un impact sur la consommation d’énergie et ainsi, permettre la création d’indicateurs de performance énergétique “IPE” associés à des usages énergétiques significatifs au sein des installations. L’édition Checking a, quant à elle, été conçue pour les fournisseurs de services énergétiques, pour les responsables énergie et les consultants afin de surveiller, d’optimiser et de gérer l’utilisation de l’énergie sur plusieurs sites. Elle offre une gamme de fonctionnalités permettant d’évaluer les consommations d’énergie, d’identifier les gisements d’efficacité et de vérifier les économies réalisées à la suite de la mise en place d’actions d’amélioration, cela via la méthode IPMVP (Protocole international de mesure et vérification de la performance énergétique, en français). Elle permet de faciliter l’obtention des certifications ISO 50001 et LEED et le développement de stratégies efficaces de gestion de l’énergie. »
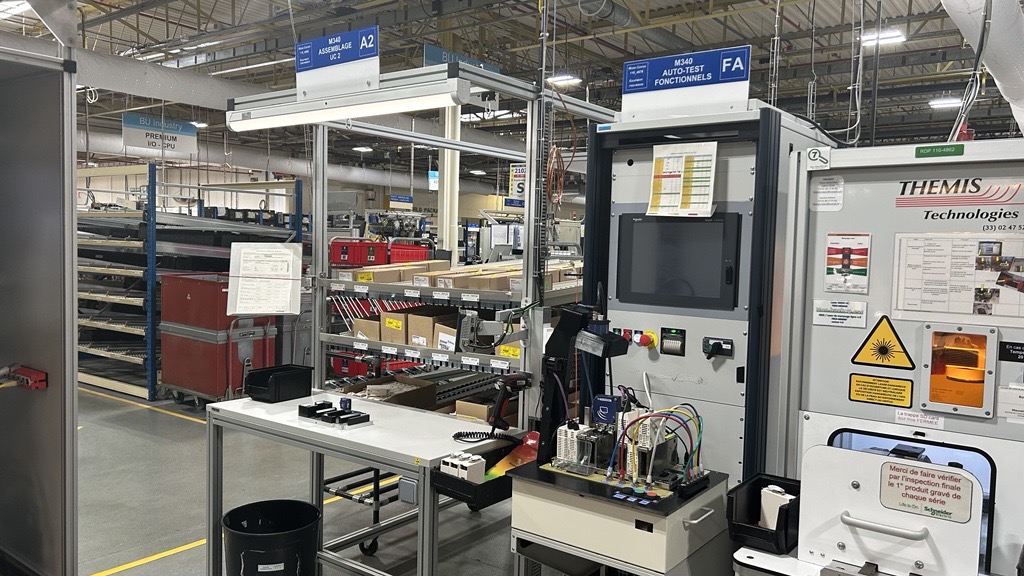
Pour Schneider Electric, Aurélien Fanget explique : « Les solutions de GTB (gestion technique du bâtiment) comme EcoStruxure™ Building Operation et de gestion d’énergie comme EcoStruxure Power Monitoring Expert (PME) vont permettre de suivre et monitorer différentes sources d’énergie. PME se positionne surtout sur les énergies, mais grâce à AVEVA nous pouvons également proposer des solutions comme le Manufacturing Execution System (MES), qui permet de piloter et gérer le processus industriel avec des fonctions avancées. Les solutions peuvent utiliser par exemple la variation de vitesse afin d’optimiser la consommation énergétique des moteurs, mais cela peut aussi concerner les installations électriques. Nous avons l’exemple de l’usine ArcelorMittal de Belval (Luxembourg) après audit de modernisation, de performances et de sécurité (MPS) visant à évaluer l’état du réseau MT, de travaux pour reconditionner 13 cellules MT avec ajout de capteurs et remplacer des transformateurs huile par des transformateurs secs issus de l’économie circulaire. Les résultats :
- des économies estimées entre 15 et 20 % sur la nouvelle ligne électrique MT ;
• 170 tonnes d’équivalent CO2économisées ;
• 26 tonnes de matériaux économisées ;
• une réduction des temps d’arrêt estimée entre 5 et 10 % grâce à la surveillance des équipements.
La troisième étape concerne le déploiement et l’optimisation en analysant dans le temps pour voir si on est en phase avec les objectifs. Nous pouvons également proposer une offre de service afin d’optimiser la régulation du contrôle commande, qui permet également de pouvoir faire de l’efficacité énergétique.
Grâce à notre plateforme EcoStruxure, nous avons un ensemble de solutions qui vont permettre de répondre aux 3 enjeux de l’industrie : enjeu de souveraineté énergétique, enjeu sociétal et enjeu économique, en permettant en particulier d’améliorer la connectivité, afin de récolter des données et les analyser pour améliorer la sécurité, la fiabilité et l’efficacité des industriels. »
Christian Amat, d’ADM21, donne l’exemple de la solution ISI Report™ : « Il s’agit d’un progiciel qui permet le paramétrage et l’édition de rapports pour le contrôle énergétique industriel, et donc de faire des bilans énergétiques. Grâce à cet outil, vous pourrez très facilement réaliser de manière ergonomique des rapports intégrant vos données, vos alarmes, mais également toute l’analytique nécessaire à vos applications afin d’améliorer votre productivité et la performance énergétique de votre activité. »
Jumeau numérique, intelligence artificielle (IA) et simulation 3D
L’Industrie 4.0 utilise le jumeau numérique, une réplique numérique d’un équipement, d’une chaîne ou d’une usine. Grâce aux capteurs et aux données remontées du terrain, il permet de simuler l’ergonomie, la productivité ou les consommations d’énergie. Ce jumeau va faciliter l’accès aux données, leur manipulation, permettre de tester différents scénarios, d’anticiper des incidents, de moduler la production ou encore d’anticiper la maintenance d’une machine. Mieux maîtriser les procédés va permettre de diminuer les consommations de matières premières, d’eau et d’énergie.
Selon Aurélien Fanget, « le jumeau numérique n’est pas encore très utilisé, mais il va permettre de gagner du temps dans la conception et la mise en service d’un équipement, jusqu’à 50 à 60 %. Par exemple, pour un fabricant de machines, notre solution EcoStruxure Machine Expert Twin permet de créer des modèles numériques de machines réelles. On va aussi pouvoir gagner en coûts de qualité jusqu’à 20 % grâce aux tests réalisés en amont et durant l’exploitation, avec le jumeau numérique. Le jumeau numérique rend la fabrication plus agile et plus flexible. L’intelligence artificielle est utilisée dans EcoStruxure Asset Advisor pour ressortir en temps réel des données et avec le Machine Learning pour faire des prévisions de panne ou de maintenance. EcoStruxure Ressource Advisor analyse des données énergétiques de l’installation pour prendre des décisions sur les fournitures d’énergie ».
La simulation 3D permet également d’améliorer et d’optimiser les process et l’utilisation des ressources et des surfaces d’une usine.
Visual Components propose une solution clés en main pour la simulation et l’émulation à destination des intégrateurs de systèmes, des fabricants d’équipements d’origine (OEM) et des entreprises industrielles.
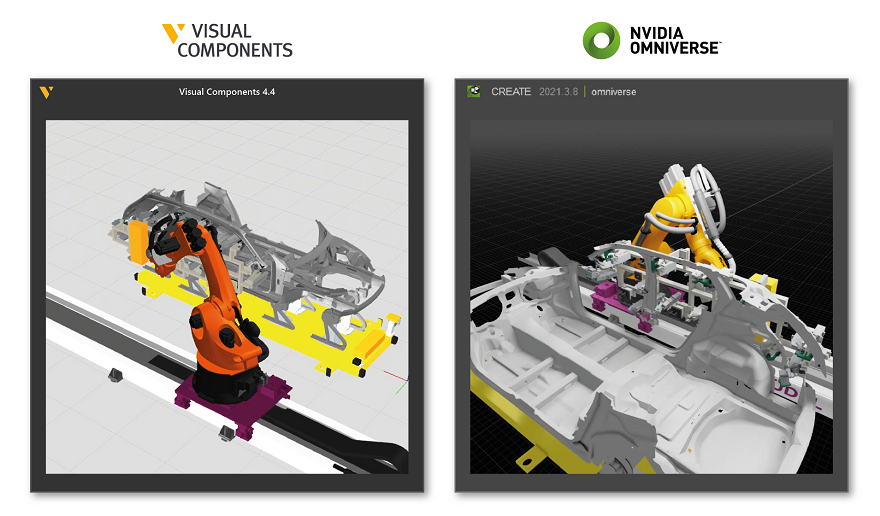
Selon Visual Components : « En matière d’efficacité énergétique, le logiciel de Visual Components aide les entreprises à optimiser la conception de leurs usines, qu’il s’agisse de réduire l’espace au sol, d’optimiser les méthodes, la production en vue de réduire les déchets ou de gérer plus efficacement les flux (AGV, AMR, chariots élévateurs et humains). Elles peuvent réaliser des gains substantiels dans leurs processus de production en élaborant des scénarios de manière simple et intuitive.
Dans le cas d’une usine existante, Visual Components permet de réorganiser les diverses cellules de travail en testant de très légères modifications : le simple déplacement d’un d’équipement dans une zone différente peut améliorer considérablement l’efficacité de l’ensemble de l’usine. Dans le cas d’une usine ou d’un atelier en phase de création, la simulation 3D offre la possibilité de centraliser les outils de production dans un espace réduit et optimisé afin de n’utiliser que l’espace absolument nécessaire et ainsi, limiter les dépenses énergétiques liées à la vie quotidienne du bâtiment telles que l’électricité, la VMC ou le chauffage. »
La 5G devrait aussi se développer, mais Aurélien Fanget note : « Au niveau de la 5G industrielle, nous sommes plutôt en analyse des cas d’usage potentiels, mais elle peut permettre de faciliter la connexion de machine à machine dans une usine et d’uniformiser les liaisons entre machines. »
Jean-Paul Beaudet