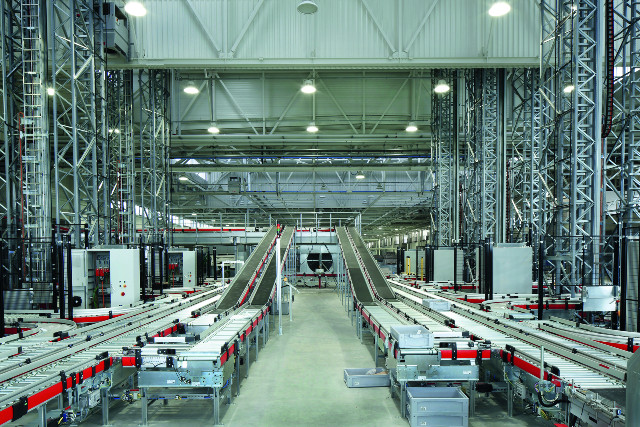
En quelques années, l’usine du futur ou industrie 4.0 est passée du concept à la réalité, adoptée aussi bien par de grands groupes de l’industrie, de l’agroalimentaire, de l’aéronautique, que par de plus en plus de PME ou ETI. Cette industrie 4.0 impose de nouveaux modèles, de la conception à la fabrication et à la maintenance, mais va aussi s’appuyer sur les outils de la Manufacturing Intelligence : une industrie pilotée en temps réel par les données, avec le recours à l’intelligence artificielle, la réalité augmentée, l’analyse prédictive, le jumeau numérique et, demain, la Blockchain et la 5G.
Le monde industriel se transforme rapidement pour devenir l’industrie du futur grâce au progrès de technologies numériques telles que l’IIoT (Industrial Internet of Things), la réalité augmentée, l’intelligence artificielle (IA), le développement des cobots (robot collaboratif piloté par un opérateur humain), les jumeaux numériques mais aussi le Cloud et l’Edge Computing pour stocker et traiter toutes les données. L’objectif étant d’avoir une usine de demain plus efficace, plus productive, plus flexible et adaptée aux besoins des clients, et moins consommatrice d’énergie ou de matériaux.
Mais comme le rappelle Gilles Pacaud, Country Sales Director de Rockwell Automation France, « l’industrie du futur n’est pas une simple accumulation de technologies ou de capteurs. Pour continuer à optimiser la chaîne de valeurs de la fabrication, les opérations doivent rassembler d’importants volumes d’éléments disparates dans un environnement cohérent et connecté. C’est là qu’entre en jeu la plateforme numérique. Celle-ci sert de lien entre ces éléments disparates. Elle se compose de technologies, de machines et de systèmes connectés et de personnes qui interagissent avec ces équipements et systèmes pour répondre aux nouvelles attentes des consommateurs en matière d’efficacité, de qualité et de personnalisation. La plateforme numérique recueille et analyse l’information provenant de chaque processus d’une usine. Elle crée ainsi un fil conducteur numérique qui permet de suivre un produit du début à la fin de sa fabrication et au-delà ».
Et, ajoute Delphine Legendre, chargée de projets marketing de Phoenix Contact France, « ce qui définit et caractérise l’industrie 4.0, c’est la communication et donc l’interopérabilité entre objets connectés. Exploiter des données qui étaient à notre disposition mais de façon masquée afin d’anticiper les aléas et faire de la maintenance prédictive. Mais aussi gagner en productivité, en facilité d’utilisation, en sécurité et en flexibilité. Autant d’informations qui vont pouvoir être utilisées grâce à des systèmes d’automatisation et de supervision intelligents et flexibles pour optimiser l’outil de production, sa maintenance, mais peut-être aussi décider de cycles de fonctionnement différents pour réagir et s’adapter à la demande du client ».
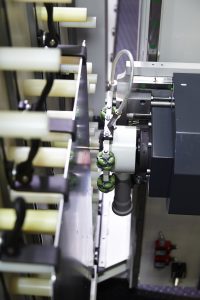
De nouveaux outils pour automatiser, visualiser, contrôler et stocker les données
Avec la multiplication des capteurs sur les machines ou sur les équipements en cours de fabrication, les entreprises disposent aujourd’hui d’une multitude de données qu’il peut être difficile d’exploiter sans outils adaptés.
Le « Manufacturing Intelligence » va permettre de rassembler toutes ces données générées tout au long de la chaîne de valeur, en provenance de sources très différentes, les saisir, les analyser et les afficher en temps réel. Cela va permettre à l’opérateur ou au responsable d’atelier de réagir rapidement aux événements non planifiés et de prendre toutes les mesures appropriées. Mais l’objectif est aussi d’améliorer la productivité et l’efficacité globale par la surveillance de la qualité des produits, la gestion automatique des stocks et des approvisionnements, l’optimisation des consommations d’énergie et de matières, la traçabilité des produits, la maintenance prédictive des machines. Le traitement de ces données doit permettre des prises de décision simples, souvent par l’opérateur.
Les résultats attendus de la mise en place de ces solutions seront :
• Réduire les durées totales des cycles de fabrication
• Minimiser les stocks d’en-cours
• Diminuer le taux de rebut des pièces
• Accroître les taux d’utilisation des machines
• Surveiller les paramètres de fabrication critiques
• Réduire les coûts énergétiques
• Suivre les performances des fournisseurs
• Améliorer l’efficacité et le confort des opérateurs
L’intelligence artificielle (IA) et la réalité virtuelle vont-elles révolutionner l’informatique de production ?
L’IA améliore les opportunités offertes par l’informatique de production et crée de nouveaux champs d’application, avec par exemple l’analyse des données historiques et la prédiction d’événements et de résultats sur la base des données. La planification de production bénéficie également des possibilités de l’IA grâce à l’apprentissage ou par la planification de scénarios complexes.
Mathieu Poissard, responsable marketing de Neovision, société de conseil et d’ingénierie en intelligence artificielle, l’affirme : « Production standardisée, multiplication des capteurs, tâches répétitives et chronophages : le milieu industriel gagnerait beaucoup en utilisant plus d’IA. L’IA surpasse aujourd’hui l’humain sur certaines tâches. De plus, l’IA permet d’effectuer d’autres tâches qu’un humain ne peut traiter seul. Elle optimise et fiabilise la chaîne de production et permet notamment de dégager du temps pour les salariés, qui peuvent se concentrer sur les tâches à plus haute valeur ajoutée. Ce peut être le cas pour un contrôle qualité automatisé et optimisé. La maintenance prédictive des équipements et des lignes de production peut aussi faire appel à l’IA. Grâce à différents signaux, il est possible de détecter une anomalie et la reconnaître comme un signe annonciateur de la défaillance future d’un élément précis. Il est donc possible de déclencher une action de maintenance spécifique avant la survenue de la panne. Nous dépassons donc la maintenance programmée et préventive, qui se base sur des rythmes d’utilisation moyens plutôt que de se baser sur l’utilisation réelle. Nous avons mené un projet de ce type pour Morphosense, société qui conçoit des accéléromètres pour les hyperstructures de génie civil : à partir des signaux des capteurs, Neovision a développé et étudié des modèles représentant les mouvements normaux des édifices pour détecter automatiquement les anomalies et dérives. »
Les entreprises utilisent également de plus en plus la réalité virtuelle et augmentée pour visualiser, simuler et développer des environnements virtuels réalistes. L’objectif est de simuler les processus de fabrication, visualiser des opérations (la maintenance, par exemple) et aussi mettre en miroir des projets de développement concrets à l’aide de jumeaux numériques. Ces jumeaux numériques utilisent les données des capteurs IIoT sur une machine pour la modéliser virtuellement et permettre d’en optimiser le fonctionnement. Cela peut se faire pour une machine, une armoire électrique, un moteur ou une usine entière. Les usages de ces jumeaux numériques ne cessent de se développer, de la maintenance prédictive au design de produits avant la construction d’un prototype physique ou la formation d’opérateurs.
Des plateformes de solutions numériques pour l’industrie de plus en plus complètes
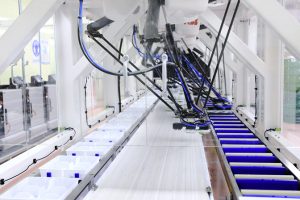
Tous les grands acteurs de l’industrie électrique ont développé une offre de plateforme de logiciels dans le domaine de l’IIoT, souvent à la suite de rachats d’éditeurs de logiciels ou de collaboration avec des spécialistes comme SAP ou Atos.
ABB propose sa solution ABB Ability, étoffée en 2019 par un partenariat avec Dassault Systèmes et ses logiciels de conception et de simulation 3D Experience, pour offrir une plateforme allant de la conception de produits jusqu’à l’activité de l’usine. ABB Ability offre ainsi un large éventail de solutions d’optimisation et d’automatisation pour améliorer la qualité et la précision des processus de fabrication. « Cette offre inclut plus de 220 applications, confie Éric Dubois, Digital Business Developer d’ABB France. Elle devient un écosystème digital-industriel ouvert accessible à l’échelle mondiale pour nos clients, partenaires et fournisseurs. ABB Ability associe une expertise approfondie du domaine d’activité et une expérience inégalée en matière de connectivité ».
Schneider Electric étoffe régulièrement sa plateforme EcoStruxure , une architecture ouverte et interopérable s’appuyant sur les technologies existantes dans le domaine de l’IoT, de la mobilité, du Cloud Computing et de l’analyse de données. EcoStruxure a été déployée sur plus de 450 000 installations et se décline en plusieurs plateformes comme EcoStruxure Machine Advisor, une plateforme de services cloud pour les constructeurs de machines, ou EcoStruxure Power 3.0 pour la distribution électrique.
Des solutions que Schneider Electric vient de mettre en œuvre dans son centre de distribution d’Évreux (un bâtiment de 43 000 m2 certifié HQE). Cette transformation du centre d’Évreux vise à améliorer la qualité des opérations logistiques, la réactivité de l’organisation locale et accroître l’efficacité opérationnelle du centre dans le cadre de son programme mondial Smart Distribution Center.
Des données que Schneider Electric propose d’échanger grâce à la plateforme collaborative Exchange pour faire bénéficier la filière du savoir-faire et de l’expertise de tout l’écosystème.
Siemens a développé sa plateforme MindSphere dédiée au cloud industriel avec des partenaires comme Atos, SAP ou IBM. Et en 2019, Siemens a créé le Digital Experience Center en partenariat avec le CEA, au sein du pôle technologique numérique DigiHall avec, parmi les thématiques, l’Edge Computing et l’intelligence artificielle avec le spécialiste français Braincube, leader mondial du Manufacturing Intelligence. Cette offre s’est élargie fin 2019 à des services numériques dédiés à la maintenance prédictive des systèmes d’entraînement : MindSphere Predictive Assistance.
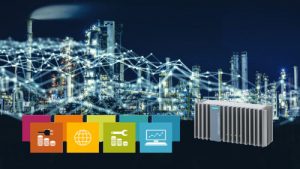
Pour aider les PMI/ETI à passer un premier cap vers la digitalisation de leur industrie,
Siemens a lancé une solution clé en main, complète, l’Edge Factory Box. Elle donne la possibilité au travers d’applications intégrées d’analyser les données pour optimiser les chaînes de production, minimiser les temps d’arrêt ou maîtriser les risques. Pour Hélène Olphe-Galliard, directrice générale de Braincube, « pour quelques milliers d’euros, elle permet aux entreprises de collecter et utiliser leurs données en temps réel au plus près de la production, pour par exemple surveiller ses paramètres critiques, être alerté en cas de dérive, suivre son TRS… C’est la solution prête à l’emploi, sur le même principe qu’une box Internet, qui permet à toute PMI/PME d’engager facilement la transformation de sa production ».
Pour Phoenix Contact, le cœur de l’industrie 4.0 réside dans la mise en réseau intelligente des process, des installations, des composants et avant tout des objets et des personnes, mais sans négliger les problèmes de sécurité. Pour Delphine Legendre, « l’aspect sécuritaire est aujourd’hui une préoccupation majeure des entreprises. Nous prenons très en amont la problématique de cybersécurité et nous accompagnons les industriels à la transition numérique, et donc la protection des données : la sauvegarde du savoir-faire et de tous les actifs de données sensibles constituant le métier ou le processus de fabrication ».
Un point à ne surtout pas négliger car la plupart des systèmes industriels n’ont pas été construits pour se protéger des cyberattaques. La transformation numérique change la donne.
Jean-Paul Beaudet