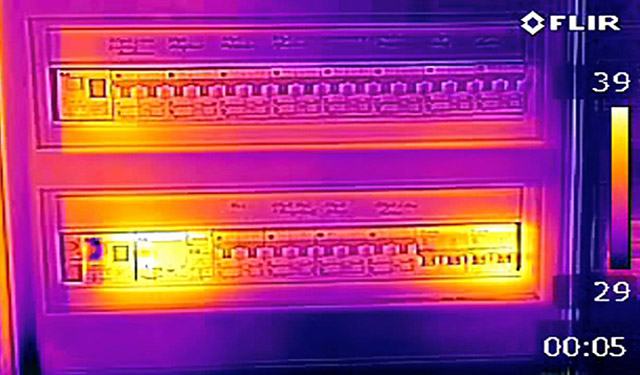
les caméras thermiques font leur apparition dans l’industrie dans les années 60. Elles sont de suite destinées à la détection sans contact pour mesurer les problèmes d’échauffement mécaniques puis très vite électrique. Elles sont depuis devenues un outil de maintenance préventive
Destinées avant tout pour un usage militaire, les caméras thermiques font leur apparition dans l’industrie dans les années 60. Elles sont de suite destinées à la détection sans contact pour mesurer les problèmes d’échauffement mécaniques puis très vite électrique. Elles sont depuis devenues un outil de maintenance préventive indispensable. Mais le coût des caméras thermiques limitait leur usage aux grandes entreprises ou aux organismes de contrôle. Depuis peu des fabricants ont sorti des modèles à prix très accessibles donnant droit à de nouvelles applications pour l’installateur électrique et les particuliers. Mais il est nécessaire de se former pour savoir mesurer et interpréter les résultats.
Contrôle des installations électriques par thermographie infrarouge
Simple à utiliser, la caméra thermique infrarouge nous révèle les problèmes thermiques, notamment pour le bâtiment en matière d’isolation et de perméabilité à l’air. Dans le cas de l’électricité, son utilisation a pour objectif de déceler les échauffements anormaux et de détecter la perméabilité à l’air des prises installées (important pour les maisons BBC).

L’électricité est une des premières causes d’incident. Pour les entreprises, un incendie peut avoir des conséquences économiques tragiques. La maintenance préventive des installations électriques doit permettre de prévenir ces risques, de garantir la sécurité des personnes et d’optimiser la productivité. Le décret du 14 novembre 1988 impose une vérification et un contrôle visuel des raccordements, des dispositifs de protection, de l’état des installations et de leur maintien dans le temps. Mais ce contrôle visuel ne détecte en aucun cas les échauffements notamment électriques. La thermographie est utilisée pour les contrôles qualité des lignes de production ou les inspections d’armoires électriques. Cette technologie permet de mettre en valeur des problèmes non visibles à l’œil nu, explique Alain Mignot pour Livingston.
La thermographie infrarouge permet la mesure de températures de surface et de déceler les anomalies et les échauffements anormaux (mauvaises connexions, surcharges, déséquilibre de phases, contacts défaillants, sous calibrage…) et de prévoir les éventuelles interventions. Les points chauds indiquent souvent l’existence de problèmes opérationnels, par exemple des pannes de raccords électriques, un mauvais alignement mécanique, une interruption dans l’isolation, une surchauffe de moteurs ou de composants. La thermographie permet ainsi de mettre en place des actions préventives qui éviteront l’arrêt intempestif d’une chaîne de production par exemple et les coûts qui en résulteront précise Alain Mignot. L’origine de ces échauffements peut être multiple : mauvais serrage, mauvais sertissage d’une cosse, équilibrage de la charge entre les phases ou bien encore vieillissement précoce du matériel type contacteurs, disjoncteurs, télérupteurs.